With their striking lattice structures, 3D-printed saddles harness the latest manufacturing techniques in a bid to offer more comfort over long distances than traditional saddles – but they also come with a high price tag.
Ever since Fizik debuted its Adaptive saddles in 2019, the popularity of 3D-printed saddles has grown, with Selle Italia, Selle San Marco and Specialized being among the brands to expand their range of saddles.
But what is a 3D-printed saddle and why do some people prefer them? Can the high price be justified?
Our buyer’s guide will explain all, so you can decide if it’s worth upgrading to a 3D-printed saddle – they tend to be a premium choice, even among the best road bike saddles.
We’ve spoken to Alex Locatelli, product manager at Fizik, and bike fitter Dan Smith from UK Bike Fit, to help answer any questions you may have.
What is a 3D-printed saddle?
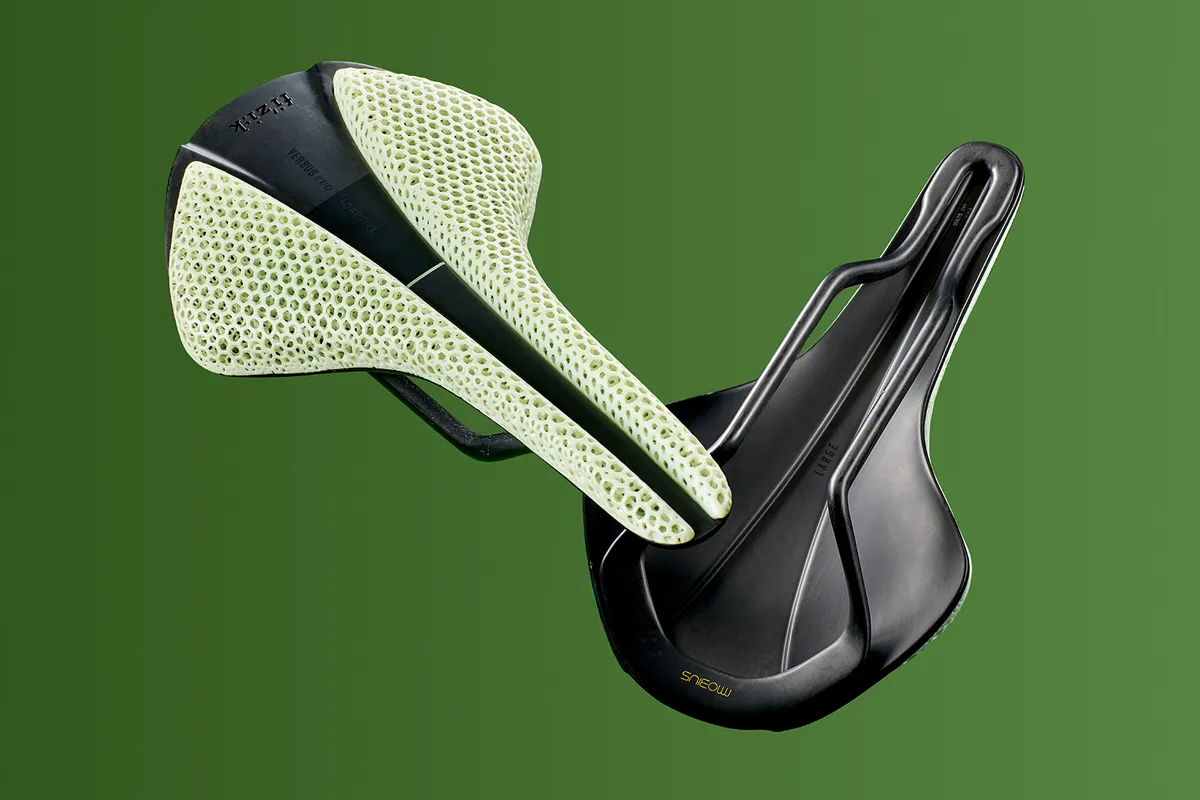
A 3D-printed saddle is a saddle with 3D-printed padding, which is glued to the base of the saddle. Only the padding is 3D-printed.
3D-printed padding is usually deeper and softer for its weight than traditional EPA foam- or gel-based padding.
Locatelli says 3D-printed saddles are made in a completely different way to traditional saddles.
Traditional saddles require a mould for the padded section (and the rails), so each time the designers want to change the design, they have to make a new mould.
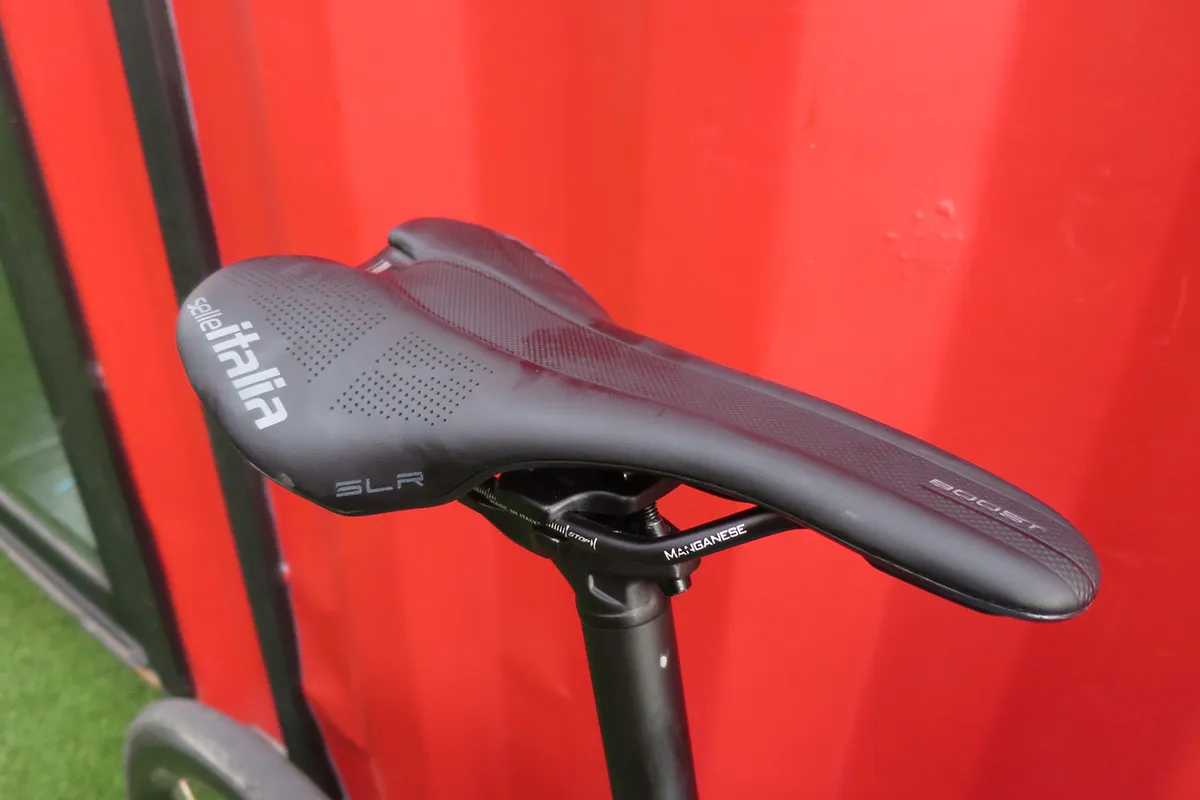
On the other hand, the padding for a 3D-printed saddle starts with a digital 3D file of the shape Fizik wants to print.
Then, its engineers add the internal structure by selecting the cell shapes, densities and zones.
The digital file is then fed into a 3D printer. The file contains data which tells the printer where to print the material: horizontally, vertically and at what depth.
A standard printer can only print in vertical and horizontal planes, i.e. in two dimensions.
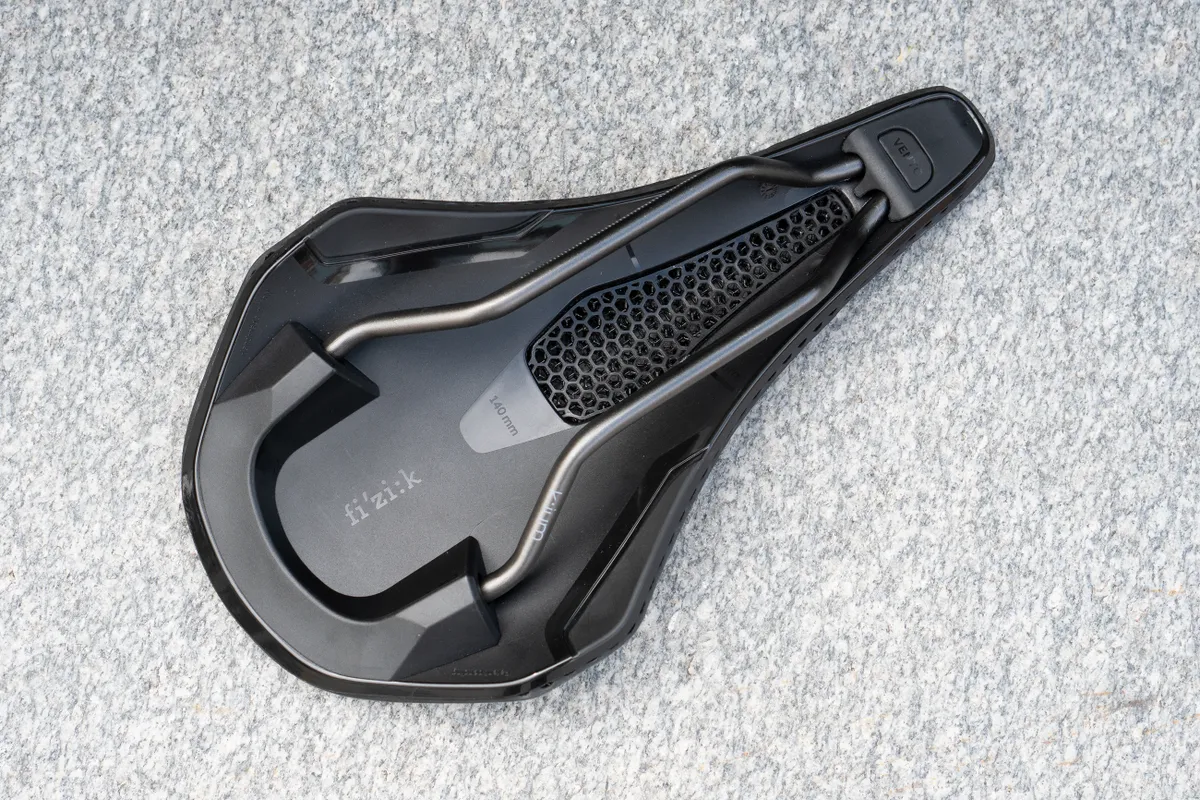
In this additive manufacturing process, the 3D printer prints layer by layer. This allows the printer to vary the thickness of each layer.
The padding for 3D-printed saddles typically has a 3-dimensional lattice of hexagon-shaped polymers. This padding is glued onto the base of the saddle ready to be tested.
The 3D-printed structure can benefit the rider by providing more finely-tuned variable padding density across the saddle, thanks to the lattice structure, while also enabling product designers to work quicker.
Fizik’s Locatelli says the brand can tweak a 3D-printed saddle design and print a new padding in minutes, allowing Fizik to test several saddle designs a day during the design and prototype phase.
What are the benefits of a 3D-printed saddle?

Provided the saddle fits you properly, which we’ll come on to, Locatelli says: “3D-printed padding can provide more comfort thanks to the mechanical properties of the material used, including better vibration dampening and pressure absorption.”
Increased comfort makes your riding more enjoyable, helps avoid saddle sores and improves performance, according to Locatelli.
“You’re moving less on the saddle to find the best spot or simply you don’t need to change position to alleviate pressure on soft tissues.
“It allows a better posture, more weight balance that, in the long run, will generate less fatigue,” he argues.
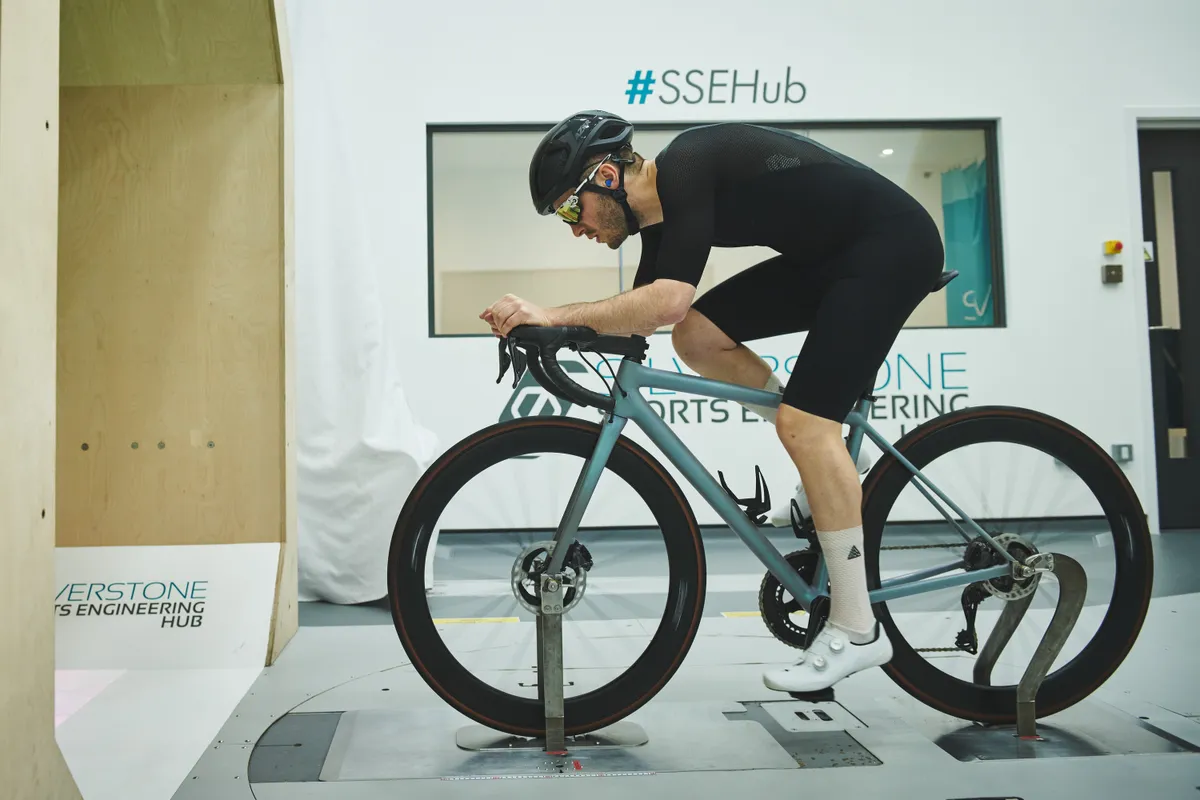
When UK Bike Fit’s Smith uses pressure mapping software on 3D-printed saddles during bike fits, he typically sees more even pressure distribution.
For Smith, this is the key benefit of 3D-printed saddles over traditional foam or gel saddles.
More pressure distribution over a saddle reduces the likelihood of “hot spots” – localised points of pressure which, because they’re often on bones, are uncomfortable, according to Smith.
The speed of the 3D-printing process benefits the saddle designers too, according to Locatelli.
“The iterations are so fast that we can now be more precise in addressing ergonomics, densities and support,” he explains.
“With traditional industrial methods, each iteration can take weeks while waiting for mould modifications.
“With 3D-printed padding, we can print multiple iterations each day.”
How do 3D-printed saddles work?
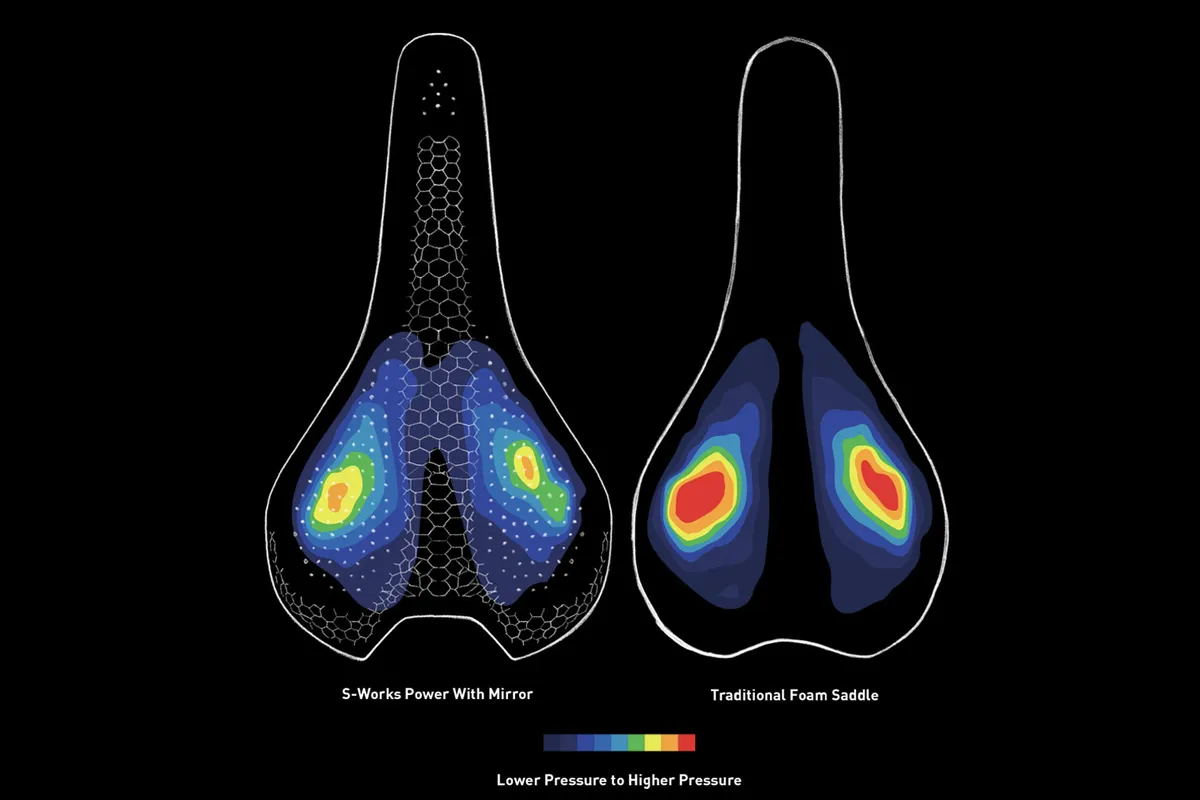
As we’ve already covered, one of the key advantages of 3D printing technology is the ability to vary padding density with more precision than a traditional saddle.
Where riders tend to place more pressure, such as the saddle wings where sit bones usually rest, the padding can be denser, says Locatelli.
On the other hand, the padding on the nose of the saddle might be firmer to provide more support when you lean into an aggressive riding position.

Locatelli claims Fizik has found that 3D-printed padding reduces peak pressure (the amount of load on the saddle where a rider rests the most weight) by 60 per cent.
Although he is sceptical about some 3D-printed saddle marketing, Smith says: “The padding is thicker and you have air instead of solid material (whether it’s foam, gel or a combination) underneath you.
“So it spreads the pressure over a wider area because there’s no firm contact on your pelvis.”
What are the disadvantages of a 3D-printed saddle?
Don’t overlook saddle fit
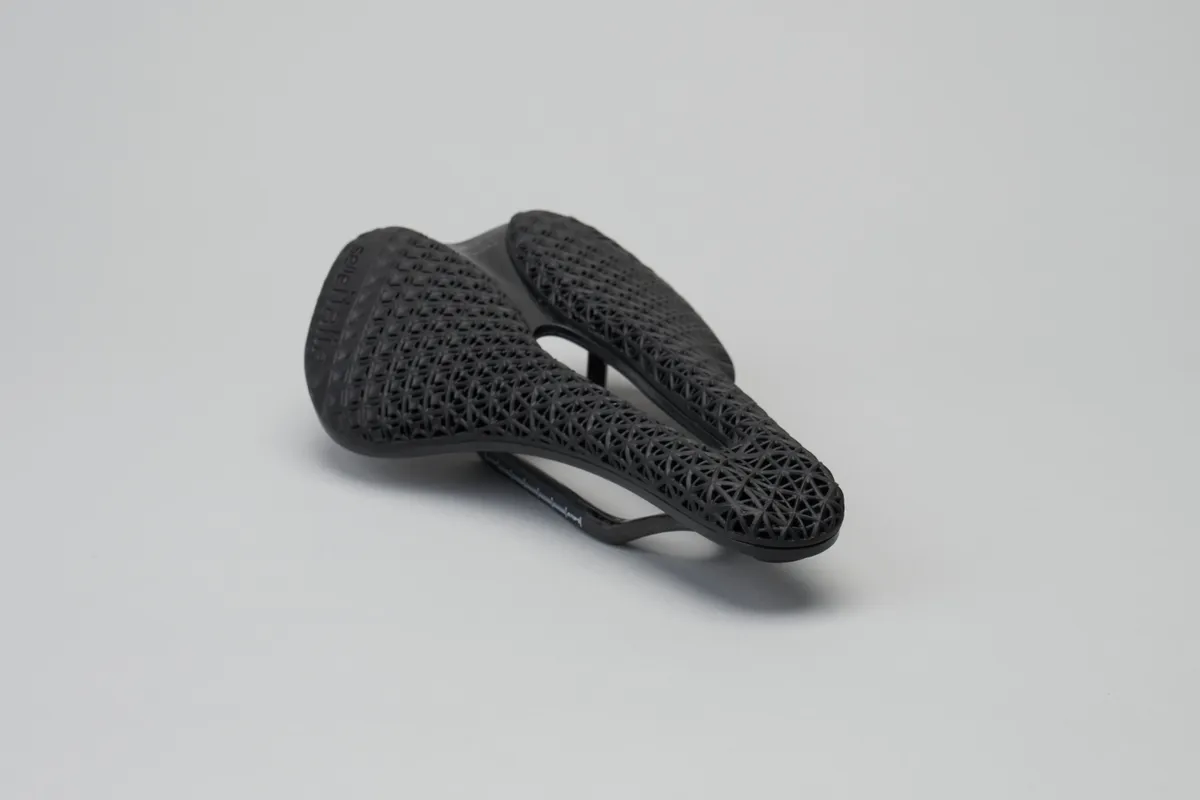
While a 3D-printed saddle can offer some advantages, buying a 3D-printed perch isn’t a sure-fire way to solve discomfort.
“3D-printed padding will not cure your problems,” says Smith.
“The padding of a saddle is the least important part.
“The shape – for instance, the width and length – and the presence or absence of a cut-out have more influence on comfort.
“To load your pelvis the way it wants to be loaded, you need the right shape saddle,” he explains.
Incorrect pelvic loading lies behind many of the most common types of pain caused by cycling.
Therefore, if the shape of a 3D-printed saddle isn’t right for you, it will still be uncomfortable.
For more in-depth advice on saddle shape, width and length, read our guide on how to choose a bike saddle.
Be prepared to pay a premium

3D-printed saddles are among the most expensive saddles on the market. This is partly because 3D-printed saddles tend to have pricier carbon rails, and 3D-printing technology is generally more expensive than other larger-scale manufacturing techniques.
But the technology is slowly trickling down to cheaper models.
For example, Specialized launched the 3D-printed S-Works Romin EVO with Mirror saddle at £390/$450 in 2021.
The Californian brand introduced the slightly cheaper Power Pro with Mirror saddle in 2022 at £290/$325/€370/AU$500.
Fizik released its first 3D-printed saddle, the Antares Versus Evo 00 Adaptive, in 2020 at £370.
The latest version (£399.99/$399.99) still tops the Italian brand’s saddle range. However, cheaper 3D-printed saddles are now available, such as the £259.99/$259 Vento Argo R3 Adaptive, although undoubtedly this is still an expensive option.

Selle Italia is another key 3D-printed saddle manufacturer and its models are similarly premium.
For example, the Selle Italia Novus Boost Evo 3D Kit Carbonio Superflow costs £399.99/$449.90. The non-3D-printed version costs £254.99/$329.90.
Are 3D-printed saddles worth it?
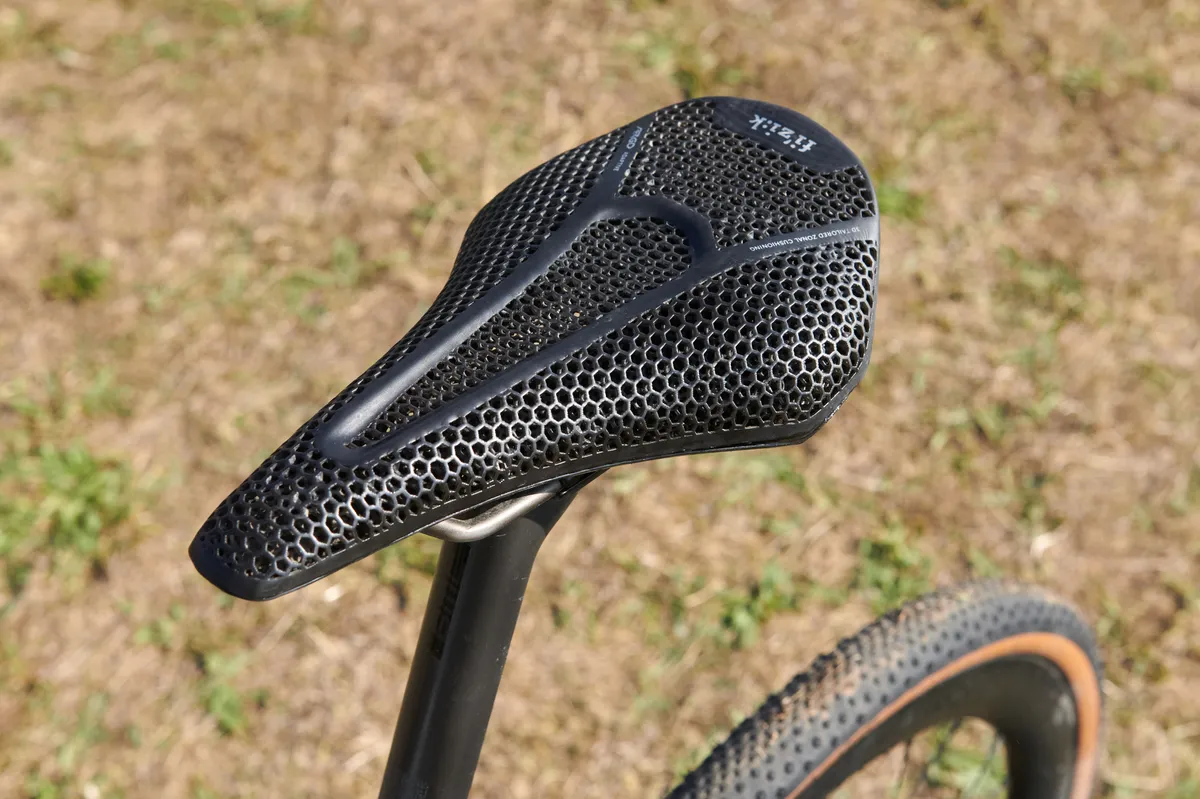
If you don’t already like a saddle, don’t bother with the 3D-printed version, says Smith.
But, for example, if you like the Specialized Power saddle, the 3D-printed version may be more comfortable because it will disperse your pressure more evenly, according to Smith.
Even then, the 3D-printed version will deliver any final improvement in comfort at considerable expense.
Ultimately, Smith advises that 3D-printed saddles are best suited to riders seeking “long-distance comfort.”
The further you ride, the greater the potential benefit. Equally, gravel riders may appreciate the vibration absorption offered by 3D-printed padding. It’s less common to see mountain bike saddles with a 3D-printed option, though.

On the opposite end to endurance riders, racers doing hour-long efforts, such as time trials or criteriums, are less likely to benefit from 3D-printed saddles, according to Smith.
“You could argue that a firmer saddle would be better,” he says.
“It could give you more support because your pelvis doesn’t bounce about and therefore better power transfer.
“You can deal with a firm saddle for an hour, particularly when producing a lot of power.
“The more power going through your feet, the less goes through the saddle,” he adds.
What are the alternatives to a 3D-printed saddle?
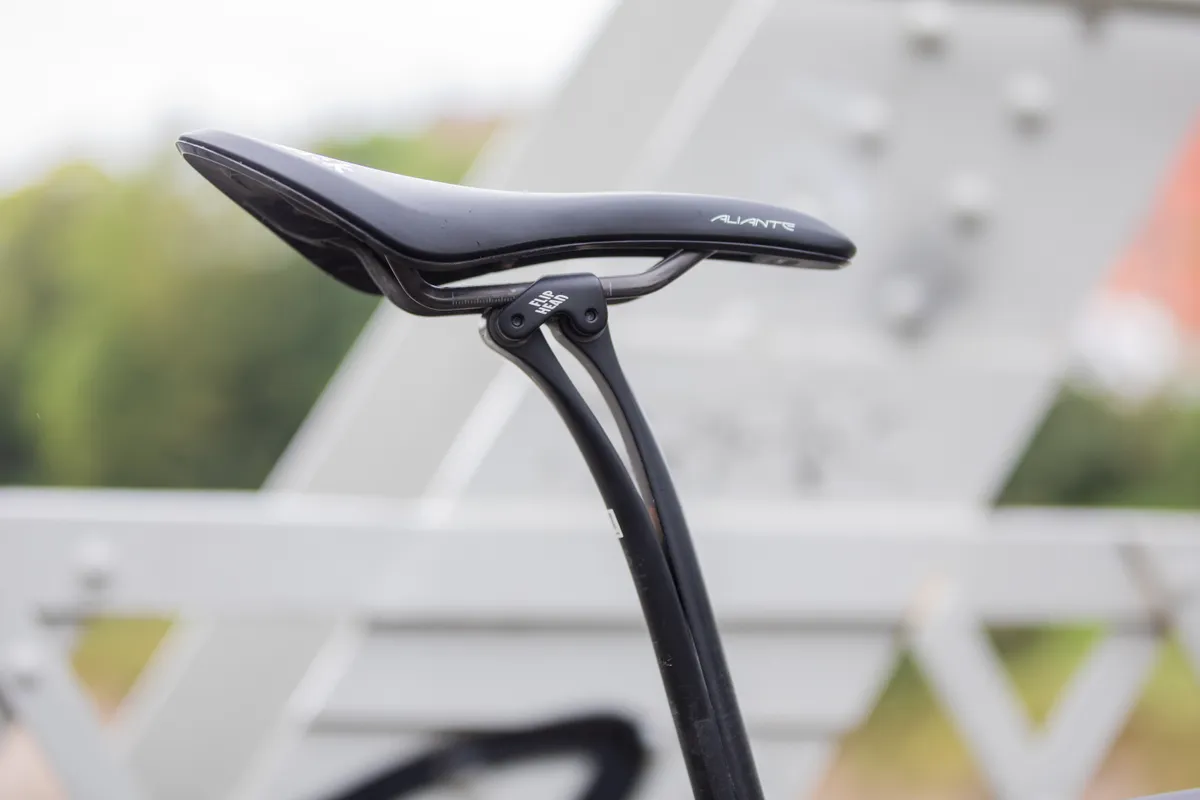
If you can’t afford to upgrade to a 3D-printed saddle or a 3D option isn’t available in your preferred shape, there are other ways to damp vibrations from the road surface and make your bike more comfortable.
Smith recommends choosing a more compliant seatpost, such as the Ergon CF Allroad Pro Carbon (labelled as the VCLS on Canyon bikes).
As a cheaper bike upgrade, he suggests running wider road bike tyres at the lower pressures that tubeless technology allows.
Tyres are “where the majority of suspension and vibration damping in a road bike come”, says Smith.
Therefore, he believes changing to higher volume tyres will absorb more vibrations than switching to a 3D-printed saddle.