Bristol-based Starling Cycles has created its first carbon frame in a radical departure from the brand’s signature steel machines, shining a light on what could be the future of carbon fibre construction.
Starling’s founder, Joe McEwan, has called upon his experience as a former composites engineer to create this full-suspension electric mountain bike frame, made from braided thermoplastic carbon tubes in the front triangle and steel at the rear.
The frame is a collaboration between Starling and the National Composite Centre, also based in Bristol, and is a test bed for a range of innovative technologies that may represent the next developments in the manufacture of carbon fibre bicycle frames.
The use of thermoplastics results in a frame that is tougher, easier to repair and less energy intensive to manufacture, according to McEwan, while offering the opportunity to improve quality control.
“With all these benefits, the project looked to develop a new high-volume, low-cost, high-quality manufacturing process for carbon fibre bike frames,” says McEwan.
A departure from steel
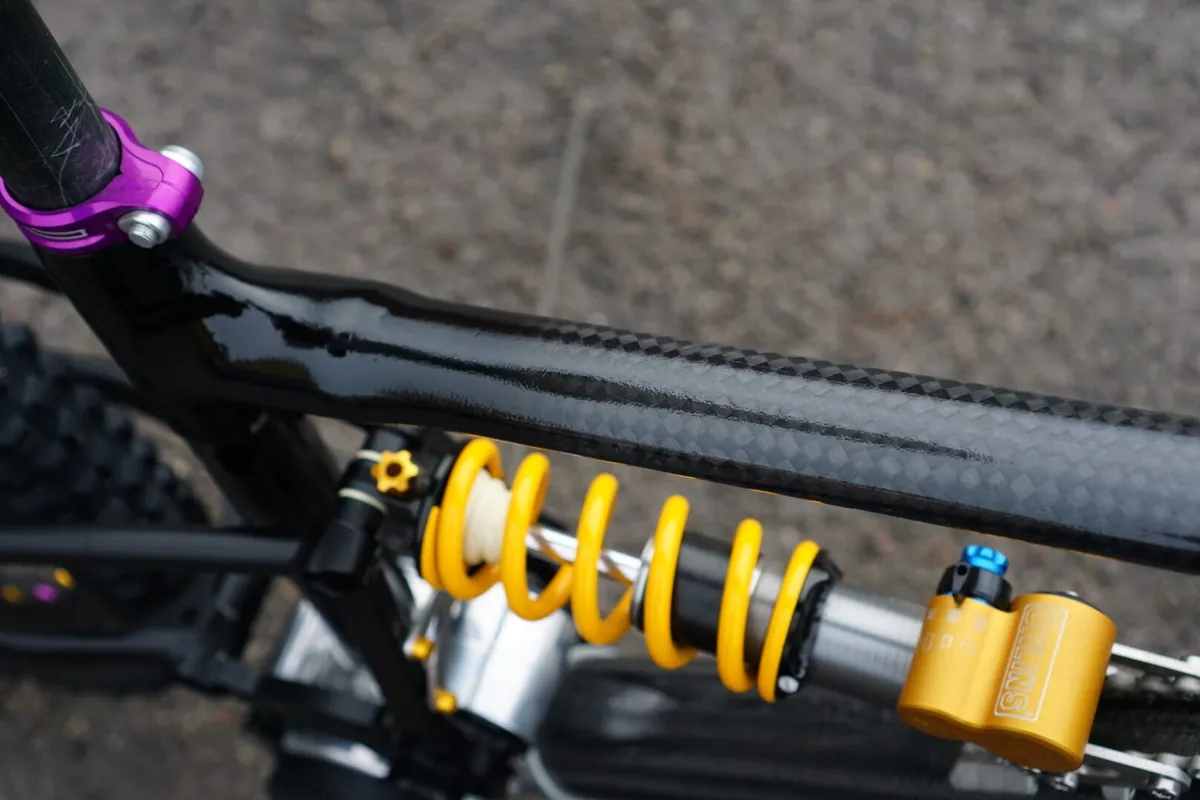
McEwan’s career has come full-circle. Initially a composites engineer in the aerospace industry focusing on carbon fibre R&D, McEwan started Starling Cycles in the shed at the bottom of his garden.
He began with the aim of building simple and elegant single-pivot full-suspension mountain bike frames made from steel, after finding inspiration in a frame-building course he attended.
Today, the brand’s range includes the full-suspension Murmur, the Twist and the Swoop, with all models available in ‘Trail’ and ‘Enduro’ flavours.
There are also McEwan’s more unconventional creations, which range from the high-pivot, gearbox-equipped Spur to the downhill, gnar-focused Sturn, with a Jack Drive suspension system. It’s a wild bike that you might remember from the 2018 video on our YouTube channel – check that out below.
Why the move to carbon?
The brand has famously avoided the use of carbon fibre in bicycles, as McEwan didn’t (and still doesn’t) believe current production methods are suitable for the quality he strives for.
However, this joint project offered McEwan a chance to develop his ideas and the result is a prototype bike that uses braided thermoplastic tubes.
The thermoplastic tubes, which combine thermoplastic resin with braided carbon fibre, come in place of the traditional epoxy-based carbon fibre that we see utilised in conventional bike frames.
The benefits of thermoplastics
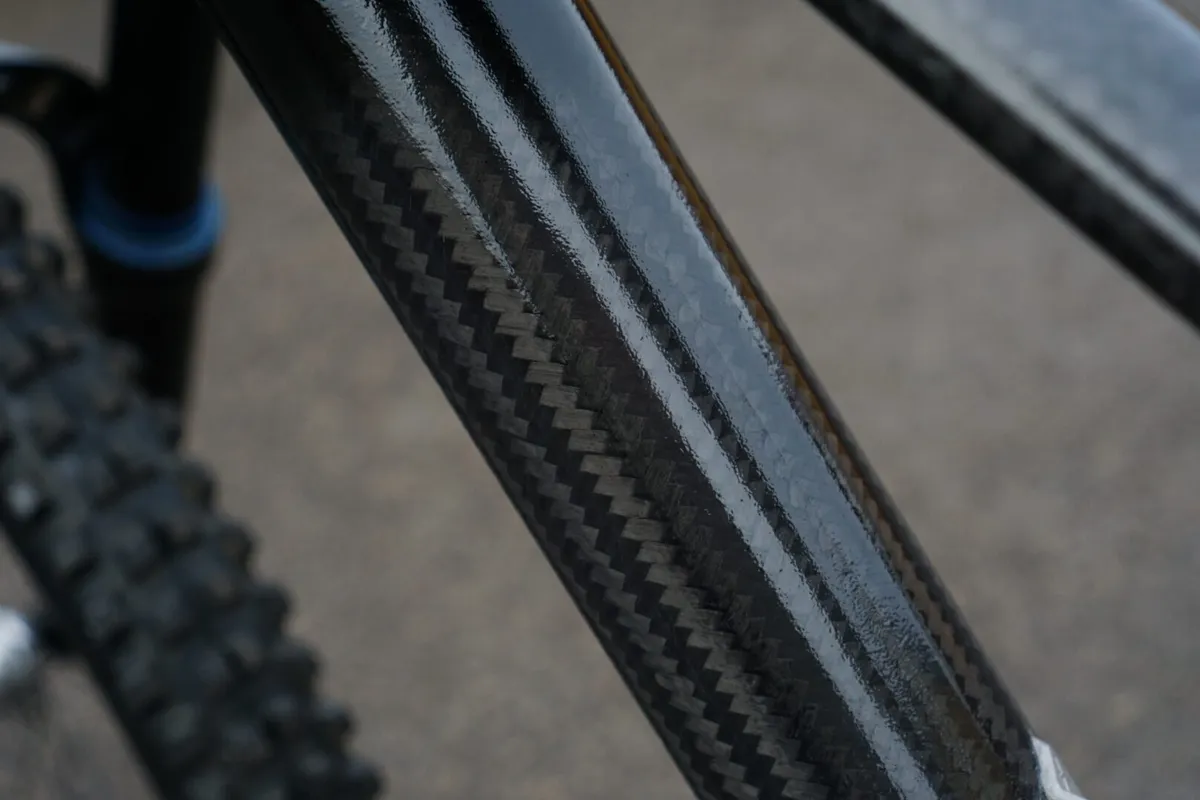
There are many benefits of bringing thermoplastics to the design of carbon fibre bicycle frames, according to McEwan.
Firstly, thermoplastic-based frames are said to be much tougher than epoxy-based carbon and can resist impact damage better, due to the increased plasticity of the material.
McEwan says the tubes are more amenable to repairs because the thermoplastic can be reformed, should there be any carbon damage in the frame’s life. However, it would require a revised process to that currently used by frame repair specialists.
There are potential environmental benefits to this method of manufacturing, McEwan says, though it’s early days for the technology.
Epoxy-based carbon fibre cannot be properly ‘recycled’, and while this is also true for thermoplastics, he says it is easier to repurpose the material.
“Theoretically, you could heat up a thermoplastic composite and remove the plastic matrix and retrieve the carbon fibres,” says McEwan. “But realistically, this would use [a] significant amount of energy and reduce the properties of both materials.”
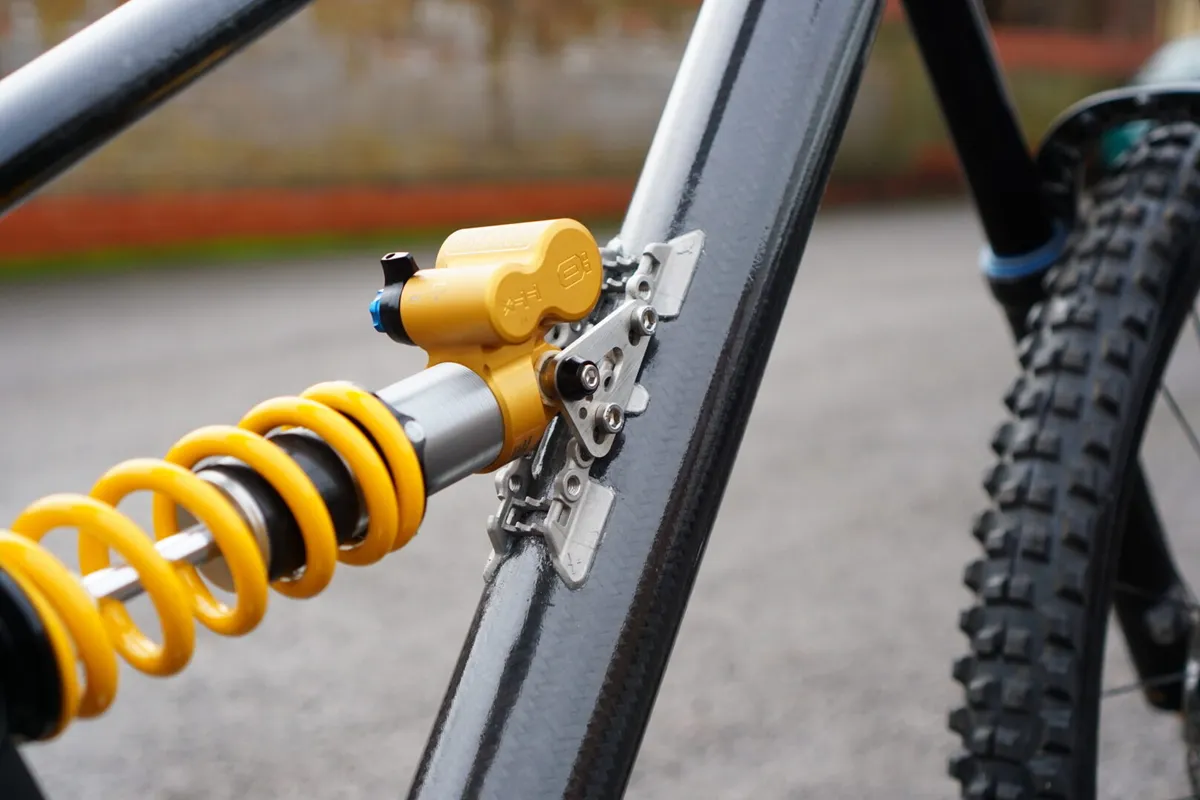
However, McEwan says old frames could theoretically be returned to the manufacturer, with the tubes then cut out and reformed into a smaller frame size.
“This is not recycling, just reusing,” he emphasises, when explaining the potential for the improved life cycle of a thermoplastic frame.
Next, thermoplastic frames require much less energy to manufacture than epoxy composites, which take longer to cure.
Finally, there can be a more meaningful QC inspection mid-way through the process.
“This means manufacturing scrap rate will be significantly reduced,” says McEwan. “I’ve heard up to 50 per cent for some epoxy carbon frames, i.e, the piles of frames going into the sea we have all seen.”
A genre-blending electric mountain bike

The concept bike that Starling has pioneered is an electric mountain bike, with the novel carbon construction used for the front triangle.
The rear triangle remains made from Starling’s signature steel, which McEwan says will increase compliance and grip when taking to the trails.
It features a Freeflow motor system and the mount is aluminium. It also features a Jack-shaft driven system, as featured on the Sturn. This adds an additional chainring to the non-driveside of the bottom bracket with a secondary chain and additional pulley. The result is you can completely isolate the suspension from pedalling forces, resulting in a more supple ride quality.
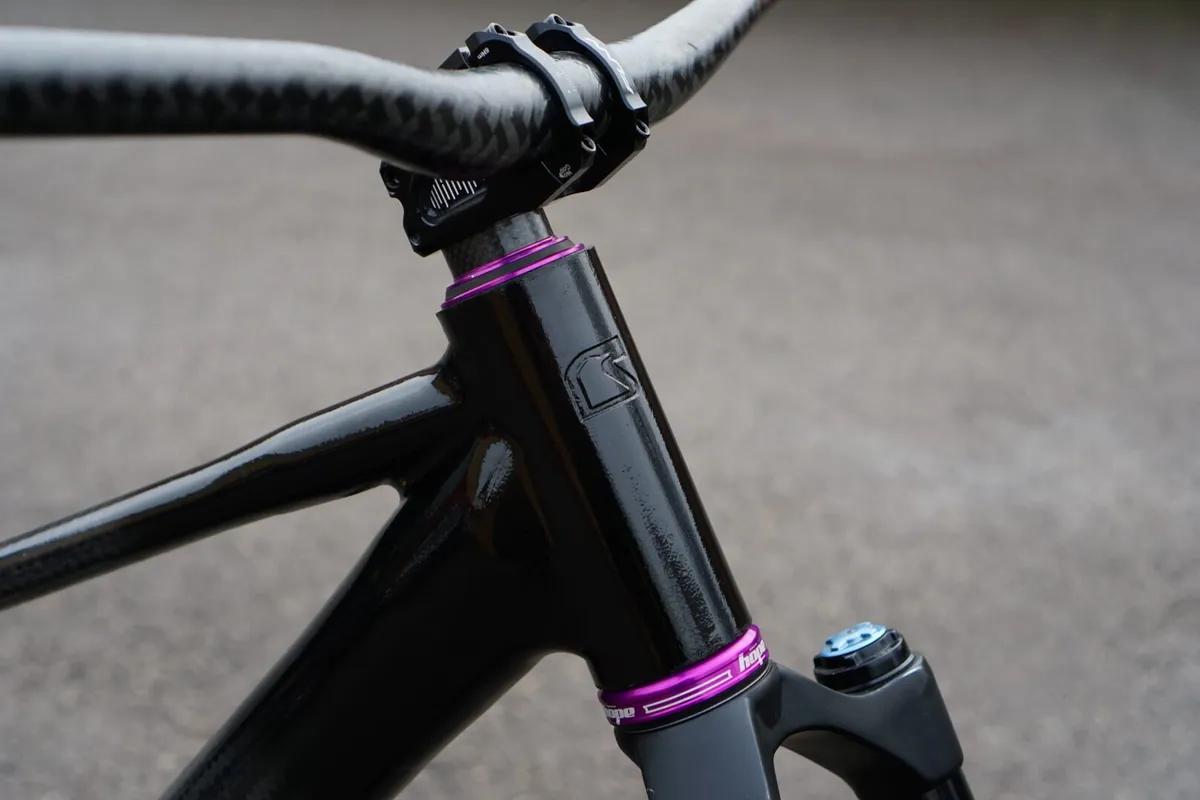
There are also intricate details such as the 3D-printed stainless steel shock mount.
The bike isn’t rideable at the moment as the lugs “didn't work out quite as we planned”, according to McEwan. The prototype bikes use 3D-printed lugs from 76 Projects for now.
Moving forward, Starling and NCC plan to further develop and refine the technology.
Is there a future for thermoplastics in bike design?

Despite the frame being a concept at the moment, the use of thermoplastics raises many fascinating questions regarding the future of carbon fibre and its specific use in the cycling industry.
The potential benefits around repair, energy use and manufacturing quality could help reduce costs, while also offering a more environmentally friendly solution than epoxy-based frames.
A greater focus on carbon fibre repair could also help keep bikes on the road or trail for longer, rather than condemning damaged frames instantly to the scrap heap, and that’s no bad thing.