Chris Cocalis launched Pivot Cycles in 2007, after leading Titus Cycles since 1991. He began his career in the bicycle business in Chicago during the early 1980s, working in the retail channel while racing BMX throughout high school. He started racing BMX professionally during his time at Arizona State University, where he majored in accounting, and helped run two successful bike shops in Phoenix. BikeRadar's Marcus Farley spoke with Cocalis about his background, Pivot Cycles and why he thinks Pivot bikes are still at the cutting edge.
In 1988, Cocalis attended the Olympic Training Center in Colorado Springs, Colorado and achieved his certification as a United States Cycling Federation Certified professional mechanic. By 1989 he'd moved into manufacturing, and started Titus Cycles in 1991.
His expertise in custom fitting and his reputation for quality, innovation, and customer service grew Titus into its position as one of the premier high-end brands in the cycling industry. Over the next 10 years, his designs were sold to and manufactured for some of the largest companies in the industry.
In addition to his innovative bicycle designs, he has been an industry pioneer in flexible manufacturing, tooling design, and cutting edge materials engineering. He has done testing and development for Miller Welding Corporation, Alyn Corp, and Gore Industries. He also serves on the component development team for Shimano, with many of the new features on Shimano's 2008 XTR directly attributed to his input.
In July of 2006, he sold his interest in Titus Cycles to Vyatek Sports, who'd been co-owners since 2001. But after a short hiatus, he's back designing mountain bikes.
BikeRadar: Tell us about your background; how did you get into making bicycles?
Chris Cocalis: I started BMX racing about the age of 13 and by the time I was 16, I was a little too big for the BMX bikes of the time. I was going through several frames a season, as were some of the other guys on our team so I designed a new "pro length" BMX frame and had a company in California build it for me. That was my first start with frame design.
In 1987, I really got into mountain biking. I had several Fat Chance's. Chris Chance was a truly inspiring frame builder and one of my favorite builders to this day. I was really into the geometry and technical aspects of the frames. It was a great time to be involved because it was the true birth of the technology side of the sport.
I had a friend teach me to braze and in 1988 I built my first elevated chainstay mountain bike frame. We even had a test in Mountain Bike Action in an article called "Bikes of the Future" alongside two Mantis frames and the Nishiki Alien. That was my start with frame building.
In 1990, I started designing cranks and bottom brackets. My bottom bracket design featured an oversize titanium spindle and two drive side bearings pushed out as close to the crank arms as possible for increased stiffness. The design was adopted by TNT racing and was featured on Specialized S-Works bikes from 1991-1995. My crank was called the Cyborg which I licensed to AC racing. That crank was used on the highest end Diamond Back bikes of the time.
In 1991, I founded Titus Cycles with two partners. I have a 17-year history that would take the entire interview, but most riders are familiar with Titus as the company I built and the products I designed. In July of 2006, I sold my interest in Titus to Vyatek Sports, took some time off and then started Pivot Cycles and BH Bikes USA in July of 2007.
Has it been exciting or nerve shredding setting up a new brand?
It's been super exciting. It's hard to believe the support we've gotten from the dealers, and riders. It's been overwhelming in a very positive way. I've made my home in our great sport and it's just awesome to see that people have welcomed me back with open arms.
What's the business structure at Pivot – who's involved and in what capacity?
We're a small company with a lot of bike experience. Our sales manager, John Bradley, has over 30 years of experience in product management and sales. He has worked at Trek, Avid, and Orbea serving as everything from product manager, to product director, to sales manager and he is an important part of our sales team along with Adam Vincent and Rob Aguero who are also passionate cyclists with a lot of industry experience.
On the product development side, we have Kevin Tisue, Bill Kibler, and of course Dave Weagle. Kevin is a talented mechanical engineer with a background in composites. He helped us launch MaxM components at Titus and was involved with me in the design of the Carbon Racer X, among other bikes. He also holds several seat post patents.The linkage seat post head design that Race Face uses is his.
Bill Kibler is a design and manufacturing expert with a long history in cycling and auto racing, and Dave Weagle is the inventor of the dw-link and many other cool cycling related inventions. We have about five others (including my wife, Cindy) that make this company go and a small group of investors, all of which are cycling fanatics.
What advice would you give to someone setting up their own bike company? Has your accounting qualification helped?
I can't adequately relay what seems like millions of details that it takes to set up a bike company. Let's just say that it's been a lifetime in the making and I am still learning something new every day.
As far as the accounting side goes, I was in the engineering program for close to three years before finishing up with an accounting degree so I have some book engineering and certainly a lot of hands on engineering, design and fabrication experience as well. I vastly prefer the creative side, but I am very dialed in on the numbers. We run a pretty tight ship in that regard; I handle the costing, and forecasting and Cindy is the CFO. She has a very strong accounting background and really keeps that side of things going so that I can focus on the bikes, which is my true passion.
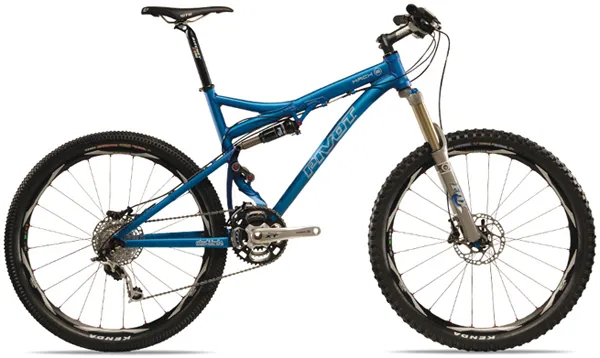
Why should people buy a Pivot bicycle?
There are a lot of great full suspension bikes out there but the Pivot's are truly at the next level. It's not often that someone in my position gets the chance to start with a completely fresh canvas. I spent a lot of time riding different bikes during my time off and took a long hard look at where we (as a sport) are at today, the advancements in suspension designs, and where we need to go in the future. My time off between Titus and Pivot was well spent and the Mach 4 and Mach 5 (along with the 429) are the result.
I have always looked at things with a healthy touch of paranoia (if there is such a thing). There is always something better coming around the corner and if we aren't constantly evolving and keeping ahead then we shouldn't be doing this.
I'm the first to find fault in a product and demand better whether it's someone else's or my own. The Pivot bikes are a result of riding the best bikes made, recognizing the positive traits and the weakness' and designing something better. It's everything from the suspension design, geometry, frame stiffness, proper fit, chain line, durability, stiffness and so on. We pay attention to the details and are very proud to have riders enjoy the product of our passion and hard work.
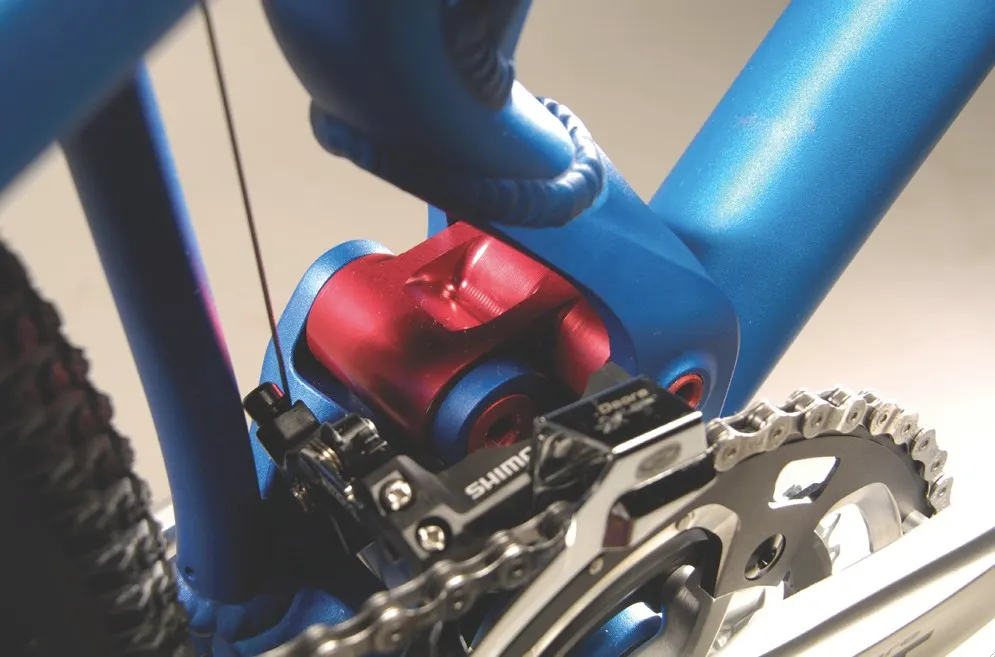
The Titus bikes used the Horst link, but you're using the DW-link for the Mach 4 and Mach 5. Why the change to a different suspension type?
It really comes down to the details and where you can take a design. Horst Link bikes can do amazing things. They are active under braking and active under pedaling plus can be built light, but there are limits. Any 4-bar is constrained to a relatively fixed travel arc. You can change the arc with the pivot locations, but it's still a constant arc.
With a dual link bike, we have greater flexibility to change that arc at different points in the travel to optimize certain characteristics at certain points. If we wanted to, it would be easy to just about perfectly match the characteristics of my previous four-bar designs, but the DW-link allows us to take things further. With the DW-link, we can make the bike pedal better and get increased traction in the beginning part of the travel as well as achieving much better square edge bump performance then a Horst-Link bike. We still maintain that active feel while keeping braking forces out of the equation.
The other big thing that has always been a goal of mine is to increase frame stiffness. With the Horst-Link it is very difficult to make as laterally stiff a rear triangle. I think we did the best job possible at Titus, but it still does not match that of our DW-link Pivots. The one-piece rear triangle and close proximity of the upper and lower links really makes for a stiff and light rear end.
The DW-link aspect brings something truly unique to the table. All other innovations aside, DW-link designs don't squat or bob under power and that's a big deal. It's the first design that really takes a riders mass and position into account. I've typically focused my efforts on the travel path, linkage rate, chain torque effect and various other driveline and braking forces on the suspension to get the bike to behave the way I want it to behave.
That's all very important, but it can all go out the window when a rider stands up and throws all his or her weight and power into the suspension. The shock companies came up with "platform" damping to help keep this at bay. It works and makes a lot of not so good bikes work pretty good, but even the most knowledgeable shock engineers realize that solving one problem with shock valving creates other problems in the way of reduced small bump sensitivity and traction.
Dave Weagle takes a different approach by placing the linkages in a position that neutralizes the effects of the rider's mass movements (anti-squat) and allows us to run much lighter shock valving so that the shock works better in bumps of all shapes and sizes while still achieving incredible pedaling performance. Also, Dave wanted me to mention that in addition to making you a faster, better rider, the DW-link will also make you more attractive to the opposite sex. What more could you ask for?

How closely did you work with Dave Weagle on the suspension? How does it differ from the Iron Horse and Ibis suspensions?
I work very closely with Dave on the suspension designs. I have certain parameters in mind when working on a new bike in regards to shock choice, ride characteristics, leverage rates and other key areas of the design and performance. I relay these to Dave and he calculates the exact pivot point placement to achieve the optimum anti-squat characteristics. I understand what anti-squat does and basically how it works, but Dave is truly the master of his domain when it comes to laying it all out and making it work.
Regarding the other DW-link designs on the market, I can tell you that they all have unique ride characteristics. As I mentioned above, I work closely with Dave on what we are looking for out of the design. The other DW-link brands on the market have their own unique vision on how they want the suspension to feel and how they design the rest of the bike. All DW-link bikes do share the positive traits of anti squat. They don't bob under power and they get great traction on climbs.
Your aluminum frames are undoubtedly beautiful looking, but are they strong in all sections?
We designed the Pivots to be one of, if not the, stiffest and strongest bikes in each respective category. Bigger is almost always better and stronger when it comes to tubes, pivots and bearings. The core of the Mach 4, 5 and 429 is our 92mm wide hollow cold forged bottom bracket and main pivot assembly. The wider bottom bracket doesn't place the cranks out any further, but it does allow for a larger diameter bottom bracket shell with the bearings inside instead of hanging off the edge of the shell.
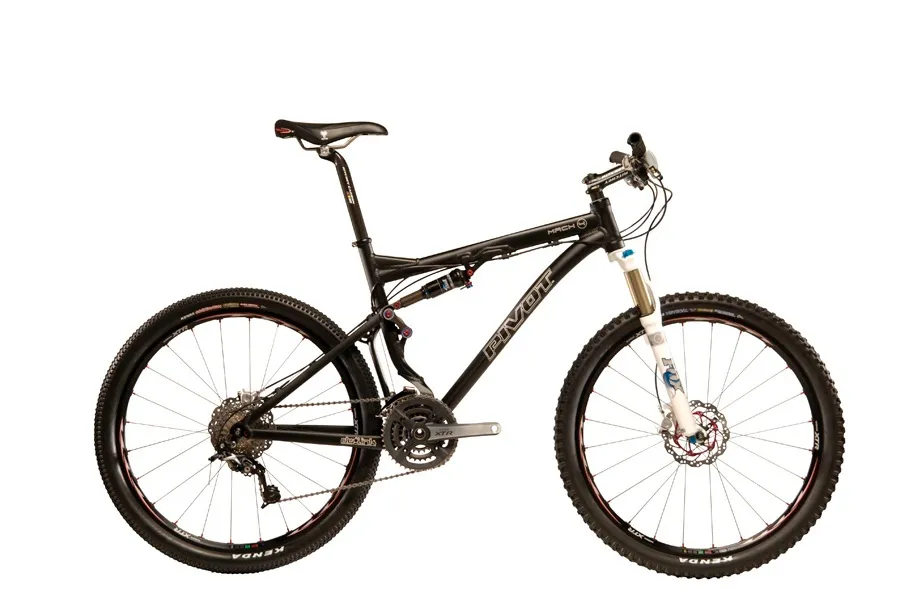
The bigger internal bearing bottom bracket shell means we can make the parts lighter, stiffer, and, of course, stronger. The 92mm shell gives us more room to utilize a larger diameter down tube which also increases strength. In addition, the wide shell gives us more space for a wider DW-link and therefore better stiffness and longevity from the main pivots.
The zero-stack style head tube is larger then a standard 1.125-inch, which increases strength and the one piece rear triangle uses large diameter tubes and cold forged parts to keep it strong in all the right places. So, yes, the bikes are strong in all sections.
Any reason you didn't go for carbon instead?
I have a fair amount of experience working in carbon and think that it's a fantastic material. There is a lot of development going on in the world of composites and its application in the suspension world. Most of the companies offering carbon models are not seeing a big weight decrease, if any, from their carbon fiber frames. They claim the big benefit as being greater stiffness, but that comes from the size of the tubes and not the material.
Others that do get the weight down suffer in durability and/or frame stiffness. I have ideas on how we can achieve both, but carbon fiber development takes a longer time and should not be rushed. We'll have an incredible carbon model when the time is right but don't hold your breath for 2009!
The Pivot bikes were conceived in Arizona, and were getting great reviews at Interbike, but have you done any testing in more muddy conditions?
Actually, good mud clearance and pivot durability were key goals when designing the bikes. If you look closely, the DW-link is way forward of where most pivots are located. On the Mach 5 and 429, we stiffen the rear triangle with the uprights so there is no need for a brake bridge up top and mud is free to pass through.
All the bikes are designed to easily clear 2.35 size tires making them some of the more open, mud shedding designs on the market. Both the DW-link bearings and the XTR bottom bracket bearings are fully sealed and housed inside the frame instead of sitting out in the elements.
From the test results, we feel that the bikes have better mud clearance then our competitors in mud (Santa Cruz, Intense, Titus, Specialized, etc.). In addition to the prototype testing, we have 40 Pivot bikes on our demo truck that tours the US, most of which has had a VERY wet spring. The bikes have been put through some seriously muddy rides.
Other than some brake pads and some cable housing replacements, none of the bikes have required a tear down or servicing of the bottom bracket or DW-link area. We use soapy water and a light washing with a hose and have experienced zero issues.
You have a dealer list for the US; when are you planning to have a dealer network worldwide?
We're partnered with BH Bikes in Spain. They have hired a sales manager for Pivot and we will have a dedicated Pivot sales force for Spain and France. We're getting ready to launch there next month and then we will be meeting with distributors at Eurobike for many of the other European markets. BH has a sales force for the UK so that will most likely be one of our next markets after we get things going in Spain and France.
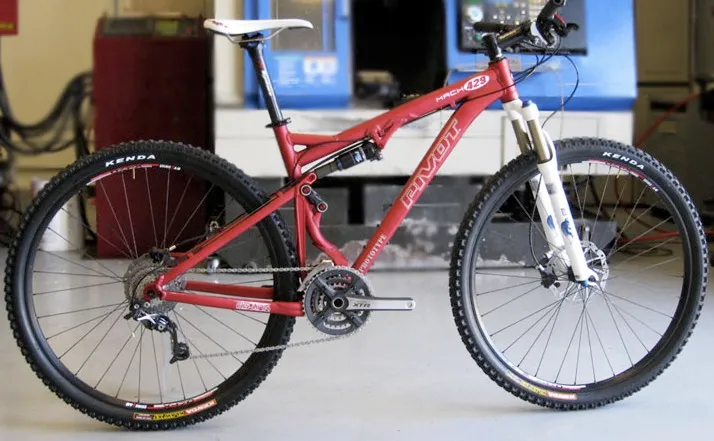
How close are you to delivering the 29ers? Any other models in the pipeline?
The 2009 29ers will begin shipping in early July, and we have a new 167mm travel bike that we will be unveiling in September at Interbike. It will have some new innovative things that have not been seen before.
What did you design on the new Shimano XTR, and what's it like working with them?
I can't take personal credit for any one thing on the latest XTR because there were a few of us from outside Shimano that were involved. I'm sure that some of the others had similar feedback. I did provide a long list of details that I felt could improve the group from the previous generation and I met with about 10 different Shimano engineers to discuss the items.
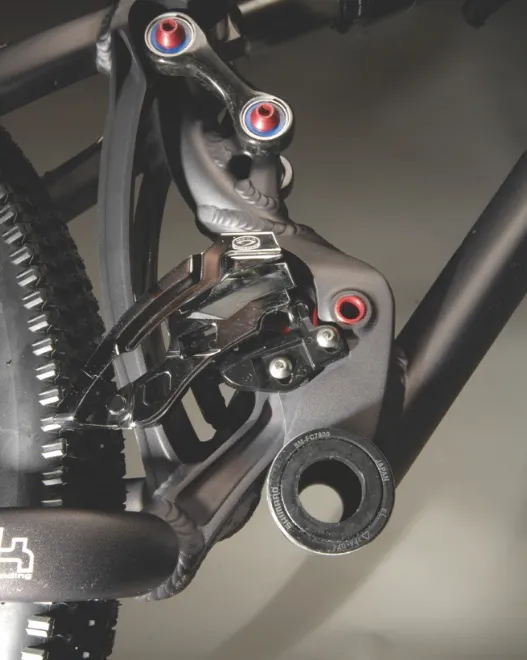
At Shimano, there is a head project engineer and then a component engineer for each item. For instance, there's a rear derailleur engineer who is different from the front derailleur engineer. There are disc brake engineers, hub engineers, etc. Shimano is an impressive company in the way they go about their product development. They're very thorough and calculated and they do a ton of research. They came up with solutions for almost every one of my suggestions and implemented most of them.
We tested early prototypes here in Arizona on a test loop that I use to develop our suspension designs. The biggest changes based on my input were the return to offering rapid fire trigger style shifters and the shift stability which has seen continuous improvements in the last couple of years.
The Dual Control system levers moved too easily and needed to be more stable so that the brake levers did not rotate out of your hands while braking. That was addressed with the new versions. Also, Shimano's previous 'light-action' designs were not working very well with modern suspension designs. In rocky conditions, you couldn't feel the positive shift and the derailleur would ghost shift quite a bit. A more solid shift that could be felt through the levers and a derailleur that had a more fixed location instead of the B-tension spring design which allowed the derailleur to really jump and move around was a problem.
One of my suggestions was stiffening and limiting the range of the B-tension spring. I think that has been achieved in a very effective manner with the new Shadow derailleur.
It was fun to be a part of the process and I think sharing information between component manufacturers and frame builders in our sport is important to help us get were we want to go with our designs. It gives the component companies a good idea of the direction we see things going and it advances the technology and the sport as a whole when we work together on projects.
What's your carbon footprint like?
I wear a size 47 (13) so my footprint is actually pretty big but I think our carbon footprint is on the small side. We have a reasonable sized facility and an environmentally conscious team of employees. We recycle almost every piece of packing material possible and are always pushing on our suppliers to reduce the size and waste in their packaging.
For a sport that is environmentally conscious by its pure nature, bike part manufacturers sure like to put a lot of parts in big fancy containers and boxes just so the box can get thrown away and the part can get put on a bike. There is definitely a better way. I don't think any of us would stop buying cool bike parts if they didn't come in some elaborate shiny box or foam filled plastic container. I'll get off my soap box now and back to the question.
The majority of our employees live within just a few kilometers (a couple of miles) from our facility. We had a shower installed when we designed the building so employees could ride into work. Almost everyone here takes advantage of it and rides their bike into work from time to time. Several commute in on a daily basis. I ride in when possible as well. I actually rode in today. It's both environmentally friendly and a major plus to live just down the street from where we work.
I know we can all be better, but I think as a company we do a pretty good job of keeping our environmental impact to a minimum.
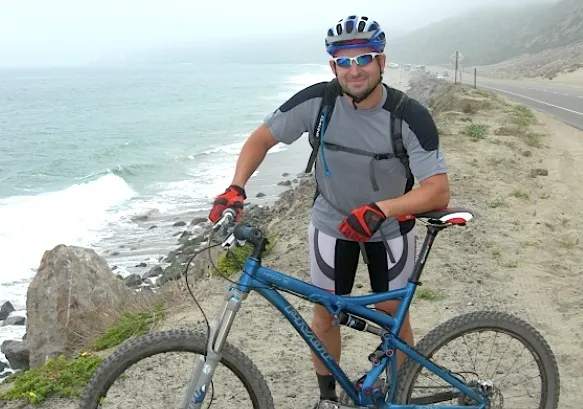
What's the best part about your job? Do you get decent saddle time?
Living close to work is great, but I would drive how ever far I needed to in order to do what I do. The best part of my job is seeing a new bike come together and riding it for the first time. I have always enjoyed that more then anything and it is even more gratifying with Pivot because we are really pushing the envelope on new ideas and technology. Everything is new from the ground up and that's really cool.
I try to ride my bike 2-3 times a week for 1-2 hours at a time to help relieve some of the stress of running a new and growing bike company.
I love working with my wife. I met her through cycling. She can typically kick my ass on a road bike or any super long ride for that matter. We do almost every activity together and we are always at our best tackling challenges together. I couldn't do it without her.
For more information, visit Pivot Cycles' website.