Cannondale call their new SuperSix EVO an evolution of the current bike. While everything about it is claimed to be better — weight, stiffness, strength, compliance and aerodynamics — they acknowledge that it’s born from the SuperSix pedigree, meaning it’s an all-round road racer. Here, Matt Pacocha delves into the construction process that's created such an extraordinary bike.
First things first: weight
A 56cm SuperSix EVO frame is said to weigh just 695g. While some manufacturers' claimed weights at launch later prove to be way off the mark, Cannondale's figure is a 'normalized' weight provided by third-party testers Zedler Fahrradtechnik.
To ensure bikes from different brands can be accurately compared, the German company use a protocol which adds or subtracts grams to/from the bare frame weight to account for items like derailleur hangers, seat clamps, headset type and even sloping frame geometry (sloping frames need longer seatposts) to make sure everything, save for the components, is accounted for.
Actual weights for the new EVO vary by graphics and paint package. The Ultimate model’s matte finish is the lightest at 727g; the clear coated frame, sold as the base model equipped with SRAM Red, weighs 750g; and the painted models that include white are 800g to 810g. The team paintjob is the heaviest Cannondale offer, adding roughly 60g over a normal clear coat.
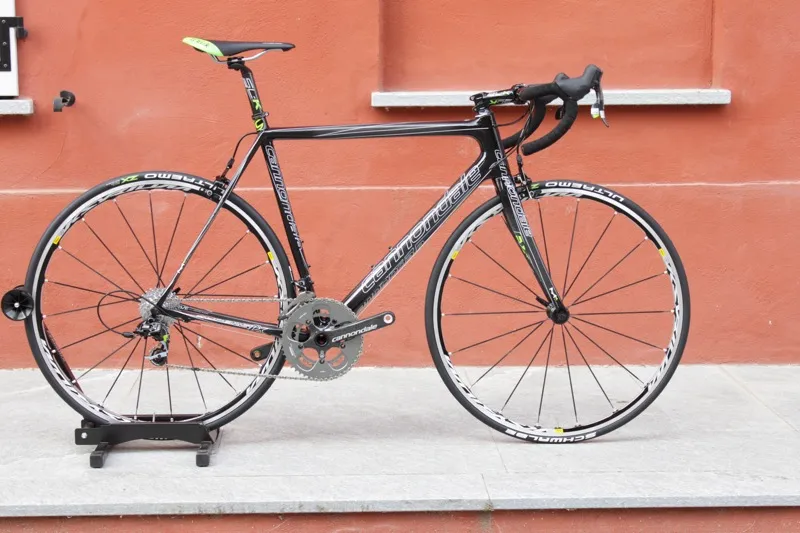
The base EVO comes in a clearcoated carbon package, which happens to be the second lightest frame, at 750g, next to the Ultimate model
“Target weight wasn't my biggest problem,” said Peter Denk, Cannondale’s director of technology. “The first bikes were very light, but the next step was bringing stiffness into the frame. We added some stiffness fibers and increased the weight of the frame a little bit, and we came up with the new stiffness-to-weight record [according to Zedler].”
Why so light, you might ask, especially since the UCI continue to enforce a minimum complete bike weight limit of 6.8kg (15lb). For amateur riders unconstrained by the governing body's regulations there are clear benefits, but there are advantages for WorldTour racers too. "It affords the [team] riders the ability to run SRMs [powermeters] all the time," Chris Peck, Cannondale’s vice president of R&D, told BikeRadar. "They also like to use alloy handlebars."
"We use the team to test product, even if we have to put weight in it for them to use it," Peck added. "We wouldn’t understand anything about the product if we made special team bikes.” Cannondale have made something special for the team, however: a range of precisely calibrated, plastic coated, steel slugs that they use to bring the weight of the new bike up to the UCI limit. They've even made slugs to account for the different weights of the wheelsets the team use, so that they can always be at the limit and not over.

The rear derailleur cable is routed internally on the SuperSix EVO
Feature wise, the EVO sports an almost all-carbon design; the only metal found is in the seat clamp, front derailleur boss and rear derailleur hanger. The headset cups and dropouts are carbon fibre, and the frame uses SRAM’s Press-Fit30 design so that it too can be made solely of carbon. But simply describing the featureset doesn’t do justice to just how much work went into the new EVO frame.
Cannondale are especially pleased with their new rear dropout design. “The EVO chainstay dropout is completely hollow,” said Denk. “Compared to one of the lightest frames on the market, only by this technology we save 34g [17g per side]. In addition to that, our fibers run along the chainstay through the outside of the dropout so the stiffness is higher than a lug type dropout. It’s a key technology as to why this frame is so light.”
“I remember very early in the project when Peter discovered this and he called me all excited and said, 'I have an entirely new concept for a dropout'," said Peck. "I said, 'that’s a really small metal or carbon part, how much weight can be saved?' and he said, ‘17g per side’. And I knew; that’s a lot. With a carbon frame at this level sometimes you’re fighting for 1g, 2g or 3g — 17g per side, that’s fantastic.”
Stiffer, stronger, smoother and more aerodynamic
While many companies can build light bikes, this often involves a compromise when it comes to stiffness or strength. Cannondale say they've avoided this on the SuperSix EVO. The new bike is said to boast the best stiffness-to-weight ratio in the business, based on Zedler archived test data. Cannondale claim a 20 percent increase in full-frame torsion stiffness over the SuperSix. According to Vand, this makes it their most precise, best descending bike yet.
Cannondale say the new bike is also stronger than the SuperSix, a claim that’s backed by the use of the brand’s Ballistic Carbon — a material introduced on their mountain bikes and used to create the super-light Flash and Jekyll. The material uses a blend of high strength fibers, which were originally developed for ballistic body armor, for its main structure. The high strength fiber is then ‘tuned’ with high modulus fibers laid in an intricate stepped manner along the sides of the tubes to offer precisely engineered stiffness attributes.
Finally, these two ‘performance’ fibers are laid over another fiber with higher elongation properties; this third, innermost layer acts as a sort of safety net which will bend instead of break if the more brittle outer layers fail. The result, according to Cannondale, it that the EVO is even stronger than their workhorse CAAD9 aluminum frame. The company say that the EVO was mostly finished a year ago and had passed all CEN testing, but because it narrowly failed one of their internal strength tests they continued working on it for another year before offering it up for sale.

The EVO's Speed Save stays are dramatically flattened
The EVO features a new design, which Cannondale are calling Speed Save, that acts as a sort of micro suspension for the bike. This engineered flex, which comes directly from the Flash mountain bike, is employed in two key areas of the bike: at the dropouts (on both the fork and chain/seatstays) and in the seat tube. “We’re not using Speed Save for rider comfort, but more for the performance of the bike,” said Peck. “The suspension in a Formula One car isn't to keep the driver comfortable… [it's] to help keep the wheels and the tires connected to the track... We want the frame and fork to have some compliance to help the wheels stay in contact with the pavement better and to give that sensation of floating.”
Cannondale claim that Speed Save improves the bike’s acceleration, rolling efficiency and cornering grip. The chain- and seatstays are ovalized so that they can bend vertically, creating a micro suspension system, while maintaining lateral rigidity. Conceptually, it makes sense — the tubes want to bend vertically in the flattened area yet strongly resist any sort of lateral bending in the same area. The fork uses a similar design, and Cannondale have also increased the curvature of the legs to promote this bending, while keeping the offset the same by repositioning the dropouts.
The Delta seat tube is also borrowed from the Flash, but it's been refined, through its carbon layup, so it can be used with any seatpost; the Flash depends on a proprietary post to meet a similar end. The seat tube is molded as one piece with the bottom bracket shell, with a lugged connection to the down tube and tube-to-tube connection with the chainstays. It changes from round at the top to oval at the bottom.

A look at the ovalized connection between the bottom bracket and Delta seat tube
High-modulus stiffening fibers are laid solely on the drive and non-drive sides of the Delta seat tube, so that it can flex forwards and backwards. This fore-aft flex, which is designed into the fork steerer and legs as well, is achieved using a sort of basket weave of Cannondale’s Ballistic Carbon at 40º and 70º angles. (Unidirectional carbon is extremely strong in tension, so if it’s laid vertically along the front and rear of the tube it won't flex; by angling it, Cannondale encourage flex in such a direction.)
By reducing key tube diameters on the new EVO, Cannondale claim to have cut aerodynamic drag by 20 percent compared to the SuperSix. The head tube taper has been reduced to 1-1/8in to 1-1/4in, which drops its outside diameter by 11 percent, the fork blades are 15 percent thinner and the down tube is 20 percent smaller, bringing the frontal area of the new bike, and thus its drag coefficient, down.
Cannondale point out that the rider is 80 percent of the aerodynamic equation and while they believe in the use of a very wide top tube, they've modified its shape to that of a subtle hourglass so the rider can bring their knees in closer to the tube to allow a knee-in pedaling position. Regardless of its aerodynamic affect, this shape will be appreciated biomechanically by many riders, especially if they pedal knees-in and tend to come into contact with large top tubes.
Engineering behind the carbon construction
Cannondale have stuck with mostly round tubes for the EVO because they believe these give a better blend of stiffness and aerodynamics than squared tubes. The frame is built in three sections: a one-piece top tube, head tube and seat tube assembly; a seat tube and bottom bracket lug component; and a one-piece monocoque chain- and seatstay unit.
To achieve their target weight, Cannondale's frame builders have to make sure the carbon layers are placed precisely and stay where they're laid during the molding process. To achieve this precision they use a preformed EPS (expandable polystyrene) mandrel that’s latex dipped. The carbon plies are laid over the mandrel, in tension so they stay placed, and the latex then serves as the expandable molding bladder in the curing process.
The sections are then joined using whatever method Cannondale have deemed most appropriate for the forces that connection or tube sees. The down tube joins to the bottom bracket via a lugged connection, which is heavy, but has purpose. By doubling the wall thickness in an engineered point on the down tube, by way of the lug, Cannondale say they can can drastically reduce tube deformation and subsequent torsional bending by even the most aggressive professional sprinters. Apparently they'd been prototyping tubes with ‘stiffening rings’ on their insides, but realized the lug has the same effect, while also serving as the connection.

A 'continuous carbon' layup is used on the EVO's PressFit30 bottom bracket shell
The chain- and seatstays are attached using a tube-to-tube process, in which the components are bonded with an industrial adhesive and then wrapped with pre-preg carbon sheets. The key, however, to Cannondale’s construction process and the way they keep weight so low and stiffness high, is their new 'continuous carbon' layup. Loops of high-modulus carbon fiber travel from the chainstay, over the joint, around the bottom bracket and then back over the connection, effectively turning it into a continuous layer. This 'continuous carbon' design is also used on the down tube lug, up the seat tube and between the seatstays and top tube.
A second new layup process is also used on the EVO frame. Cannondale's ‘graduated layering’ process involves the use of overlapping carbon stiffening layers along the sides of the tubes. These stiffening layers don't have common starting and ending points, rather they're staggered and precisely built up in areas where loads are the highest. For example, they may start as just one ply at the end of the tube and build up toward the middle where the tube needs the most help resisting lateral and torsional flex.
Key to the system: Cannondale’s force maps
The EVO’s low weight and high claimed strength is the result of using the minimum amount of material in the most efficient way possible. To make sure the bike would stand up to real-world riding forces, Cannondale created 'force maps' using two databases that no-one else in the industry has access to. These contain over 30 years' worth of lab testing and data acquisition, including feedback from Liquigas-Cannondale team riders.

Ted Ciamillo's carbon Gravitas brake and the EVO's 'Thinline' seatstays
The maps not only show typical load mapping but the direction in which the forces are traveling through the tubes. This allows Cannondale to precisely specify the carbon layup schedule, tube shape and size, all of which are then tested using FEA analysis and in the lab before heading out under riders for on-road testing.
“We've always been obsessed with testing, efficiency, building the best product for our professional athletes,” said Peck. “We spend a lot of time measuring forces on a bike. Our testing lab can simulate up to 10 years of life in just a couple of days."
The future, now
In addition to the frames now in production, Cannondale have produced a version, which Denk is currently riding, that has a weight of just 630g. This weight is achieved through an entirely different layup and new material that Cannondale were remaining tight-lipped about.
At this time Cannondale have no plans to sell this model because the material and the lay-up placement tolerances are too costly to allow any sort of large-scale production. “It’s far enough along that it was worth sending to Zedler,” said Peck. “Maybe in the future it'll make it to market, but at the moment we made it as an R&D frame to show ourselves what we’re capable of and what we can consider for the future.”

Peter Denk's R&D model EVO weighs just 630g, with paint, graphics and all of its bits