We’ve already ridden SRAM’s XX1 group and as you might imagine, there was a lot of engineering that went into creating this groundbreaking drivetrain.
We covered XX1 components in their prototype form and were recently invited back to SRAM's European headquarters, located in Schweinfurt, Germany, to learn more about the development of XX1 and spend more time ridingthe production versions of this group.
What follows is a breakdown of the development and technologies of each of the components that make up the XX1 group.
XX1 Rear Derailleur: Resurrecting the Straight P
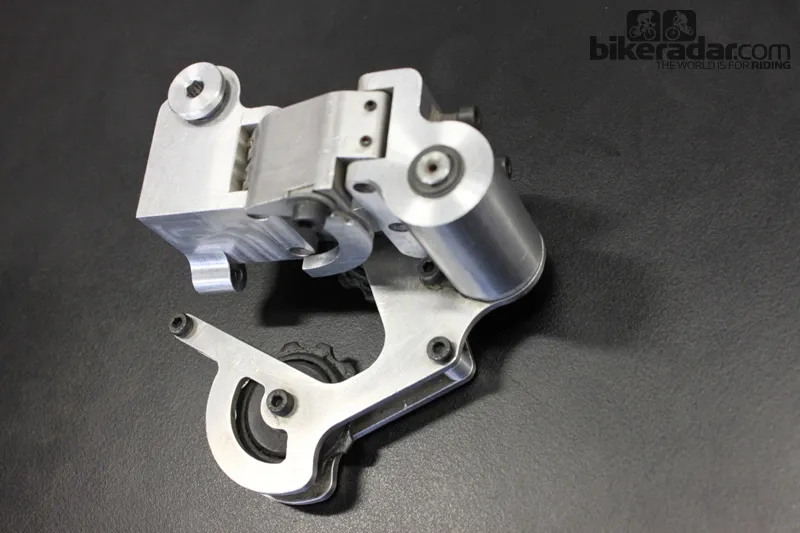
The first prototype of the XX1 rear derailleur
While development of the XX1 group began approximately three years ago, the rear derailleur was designed more than eight years ago. It began life as a project totally unrelated to XX1. The prototype rear derailleur was built with two very disparate ends of the cycling market in mind—downhill and urban bikes.
The most notable feature of this early prototype is that the parallelogram linkage only moves in a horizontal plane. The benefit of having a derailleur with a linkage that can only move in and out is that ghost shifting is minimized, even without a clutch system.
The drawback to this design, dubbed “Straight P,” is that it only works on drivetrains with a single front chainring. The lack of vertical movement does not allow the derailleur to “grow” to accommodate large changes in chain length that accompany having two or three front chainrings. On a derailleur with a horizontal parallelogram, the fore and aft movement of the derailleur’s cage must do all the work.
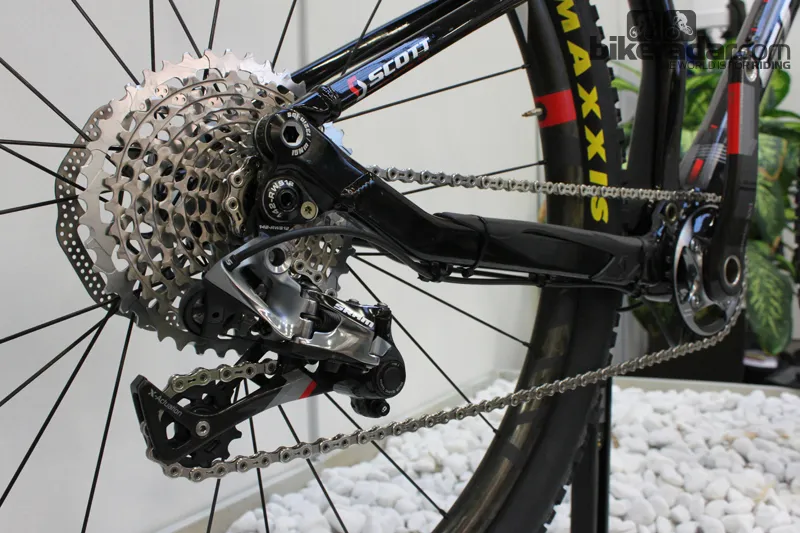
Full production version of the XX1 rear derailleur
This idea was resurrected for XX1. A type 2 clutch mechanism was added to damp the movement of the cage to further reduce unwanted movement. In terms of construction the XX1 derailleur is very similar to the XO model, with a few notable exceptions. The XX1 derailleur’s pulleys use 12 teeth, rather than 11; this helps to increase the derailleur’s chain capacity. SRAM also included a pulley wheel, which guides the cable into the derailleur. This wheel, along with the Straight P design, leads to a lighter shift action than one feels with SRAM’s 10-speed drivetrains.
XX1 Cassette: Why a 9 tooth cog failed
Following the development of the derailleur, the next step in the development of XX1 was figuring out an acceptable gear range. Early 10-speed prototypes had a 9-36 tooth range. Testing proved that a 9 tooth cog was too small to be pedalled comfortably. Such a small cog caused a shuddering sensation when pedalled under load. This is due to a phenomenon known as the “polygon effect,” which results from variations in speed as the chain transitions from one cog to the next.
“The smaller you get, the bigger the polygon effect,” said Henrik Braedt, a design engineer who worked on the development of the XX1 cassette. This effect exponentially decreases relative to the number of teeth on a cog. The addition of one tooth, along with carful machining of the tooth profile mitigated the polygon effect.

The cassette starts its life as a block of torqued steel
The next issue came from the other end of the cassette—a 36 tooth was not large enough for most riders to pedal comfortably. The solution was the addition of the 42 tooth cog. Many of the lessons learned from developing the Red and XX cassettes were applied to XX1. 10 of the 11 cogs are machined from a single block of tool steel. Manufacturing begins with a bell-shaped forged blank. This blank is placed onto a lathe that removes a significant chunk of material and leaves the blank with a stair step profile. Next, a CNC machine removes more material by carving the teeth, shift ramps and the 16 pins that are used to secure the 42-tooth aluminum cog to the steel cassette body.
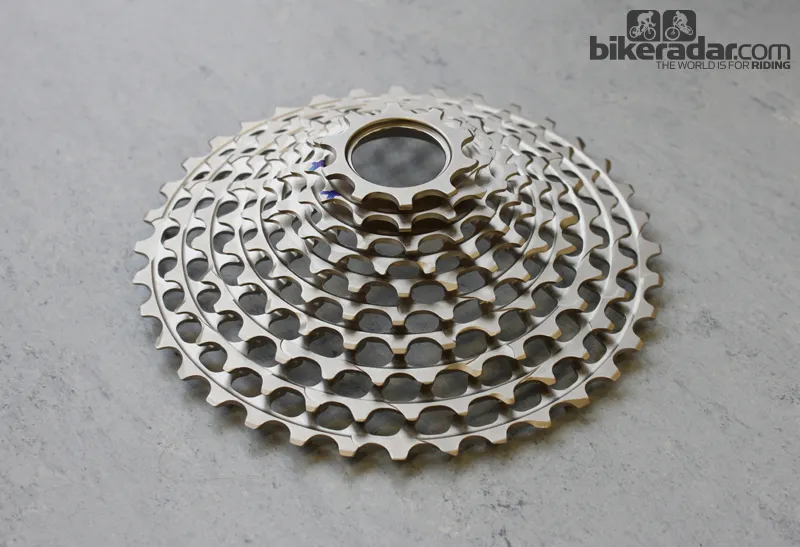
A CNC machine removes a significant amount of material and cuts the ramp and tooth profiles
Manufacturing the XX1 cassette is extremely labor intensive, machining takes approximately three hours and tolerances are checked at each step in the process. When finished, the cassette’s weight belies its large size: an XX1 cassette weights only 260 grams, 52 grams more than an 11-36 XX cassette, and 12g less than an 11-36 Shimano XTR cassette.
Currently, the XX1 cassette is only available in a 10-12-14-16-18-21-24-28-32-36-42 gearing. The XX1 derailleur can accommodate an ever larger, 44 tooth cog. It’s a safe bet that SRAM will be offering this configuration in the near future.
XD Driver: Redesigning the freehub

XD Driver on paper
SRAM’s engineers may have found the gearing they wanted, but another problem remained: a 10 tooth cog is too small to fit on a standard freehub body. A new freehub design was needed in order to make it work.
First and foremost SRAM wanted to ensure that this new design would have a minimal impact on existing rear hub technologies, with no requirement to change the design of the hub body, bearing placement, axle spacing or frame design. In fact, all that is required for most hub manufacturers is a few additional machining steps to remove material from existing splined freehub designs.
SRAM took advantage of this redesign to improve on what the company’s engineers felt was a dated system with loose tolerances. The XD driver eliminates any play between the cassette and freehub body. Such play can cause marring of aluminum freehub bodies and degrade shifting accuracy—a problem that becomes more significant as more cogs are added to a cassette.

XD Driver freehub
The XD retains a portion of the current splined interface, but adds threads on the outside of the freehub body. The X-Dome cassette has an internal sleeve that acts like an integrated cassette lock-ring. To install, one simply places the cassette on the driver body and uses a Shimano lock-ring tool to spin the internal sleeve onto the freehub’s threads, securing the cassette in place.
In an industry awash in competing standards it’s refreshing to see a company develop a new technology that places an emphasis on minimizing compatibility issues. The motivation was less of an act of altruism than it was a sound strategy to ensure that this new freehub standard would gain widespread acceptance. To this end, SRAM has made the technology open to all hub manufacturers who agree to follow the tighter tolerances the XD driver body requires. The manufacturing details and a list of companies who have signed on to XD driver standard can be found at www.xddriverbody.com. This list currently includes Mavic, DT Swiss, Bontrager, Specialized, Syncros, Easton, Stan's, Hope, FRM, Tune, Novatec and Crank Brothers.
XX1 Chain: Size matters
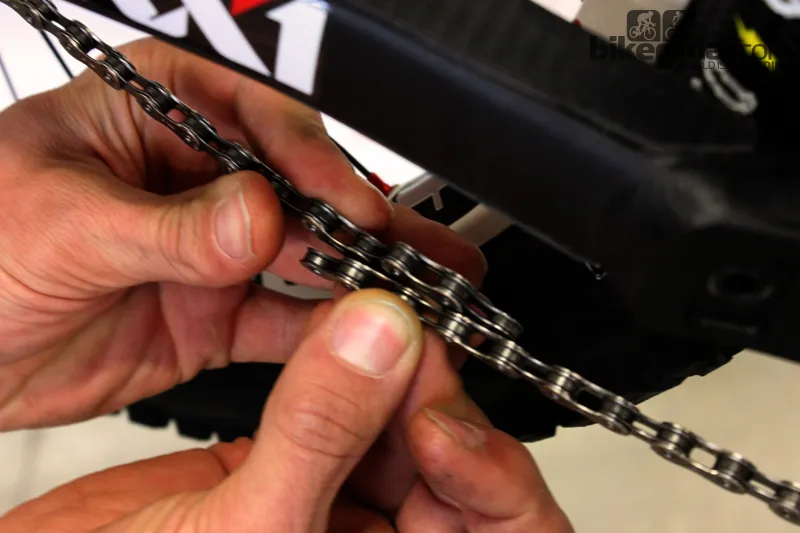
Chain sizing is critical
The first question most consumers ask when companies increase the number of speeds on a drivetrain is “how will this affect durability and longevity?” When going from 10 to 11 cogs SRAM made a point of making the chain as robust as possible; the company claims an XX1 chain is stronger than its 10-speed counterpart. An XX1 chain has the same internal width as a 10-speed chain, though the outer plates are slightly narrower to accommodate the tighter spacing of the 11-speed cassette.
Proper chain sizing is critical to the performance of XX1. When sizing SRAM chains, the general rule of thumb is towrap the chain around the big ring and biggest rear cog (without routing the chain through the rear derailleur) and add two links. In the case of XX1, SRAM’s engineers recommend adding four links to accommodate the cassette’s wide range and to allow for a bit of chain growth, which is common in many full suspension designs and can affect shift accuracy if not taken into account.
XX1 Chainring: Minimizing play
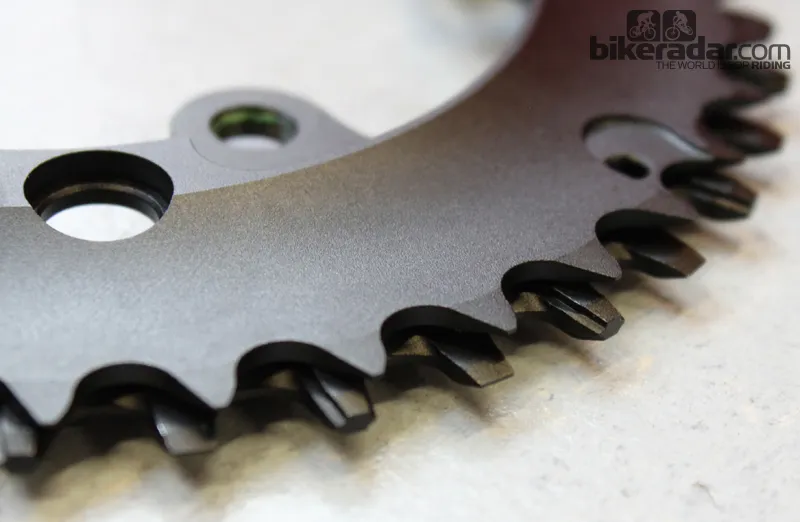
Compared with a traditional multi-speed chainring, an XX1 ring has taller teeth with a squared-off profile to minimize the likelihood of unwanted derailment.
SRAM’s engineers used video capture to analyze how chains derailed from chainrings. They found one of the most common causes was side-to-side movement, which lead to the chain coming off the top off the chainring as if by shifting. The X-Sync tooth profile reduces side-to-side movement by “snugging up” the interface between the chainring and the chain’s outer plates.
The tooth profile of an XX1 chainring is also taller and wider than that of a chainring designed with shifting in mind. XX1 chainrings will be available in 28, 30, 32, 34, 36 and 38-tooth options. SRAM claims that with a properly-sized chain a rider should be able to go one size up or down from the chainring they are running without need to replace the chain.
XX1 Crankset
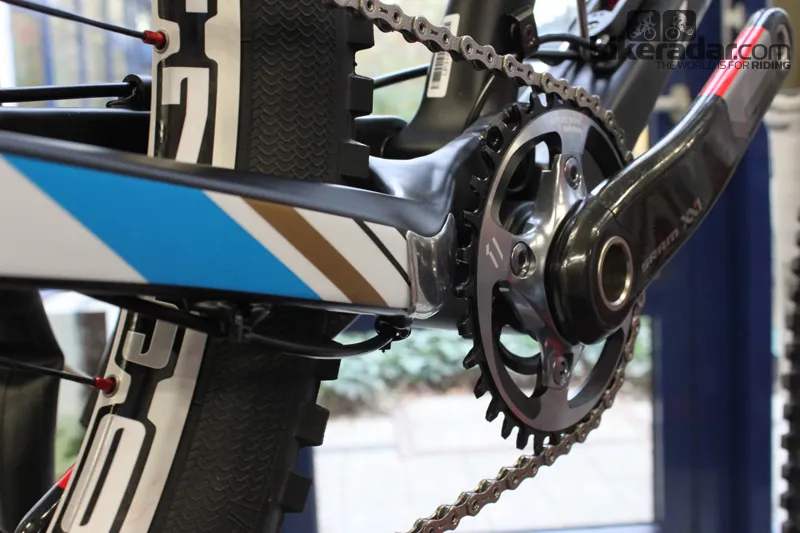
The XX1’s crankarms are the same as those used on SRAM’s other carbon cranks. The bolt circle diameter (BCD) is 76mm, which will accommodate all six chainring sizes and make swapping rings an easy task. The XX1 crankset weighs approximately 650 grams with bottom bracket
XX1 Shifter

SRAM is offering both trigger and Grip Shift options with XX1. Internally both are very similar to their 10-speed counterparts. While we have not had a chance to test the XX1 version of Grip Shift yet, it looks very promising, as it will allow riders the ability move from one end of the cassette in rapid succession.
Sum of the parts
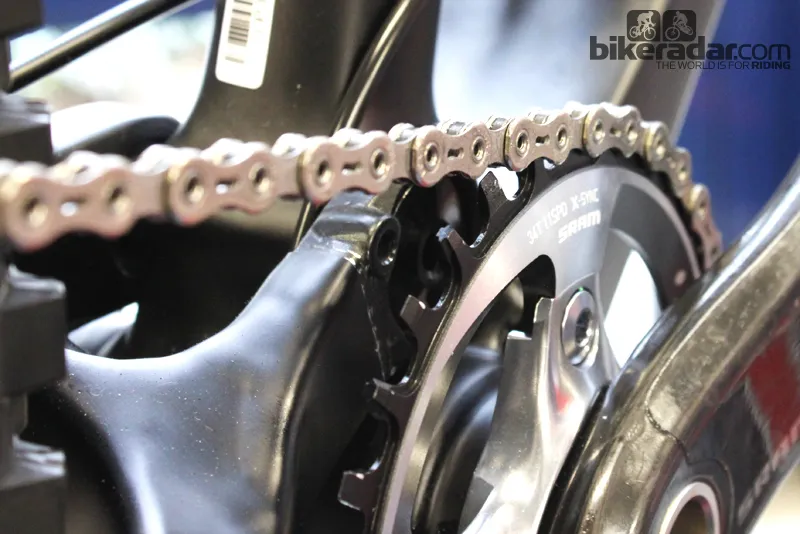
SRAM readily admits that a single chainring setup is not for every rider. The company does not see XX1 replacing two- and three-ring drivetrains, but rather, giving riders and bike companies another option to choose from.
As a group, XX1 is lighter than SRAM’s flagship XX group. Each of the parts in XX1 is actually heavier than their 2x10 counterparts, but the fact that XX1 does away with a chainring, front derailleur, front shifter, along with the associated cable and housing, results in a net loss of approximately 200 grams. Complete XX1 component groups are expected to be available in the coming weeks. Pricing is set at $1,449 for the complete XX1 group, making it more expensive than X0 but less costly than XX.
On the trail, the combination of technologies designed to keep the chain in place result in a drivetrain that is eerily silent and utterly unflappable while shifting under load. The shift action is noticeably lighter than SRAM’s 10-speed systems. This is particularly nice, as it reduces the affect of the SRAM’s Type 2 clutch mechanism, which increases the amount of force required to make a shift in two and three chainring setups. We had no problems with chain retention, though the cross-country trails around Schweinfurt were not the best proving ground.
We have an XX1 group headed our way for a long-term test.