With Trek's Project One program, riders can select not only the components but the frame and wheel color scheme as well, choosing from 18 different Trek machines. While these Project One bikes represent less than one percent of Trek's approximately 1.5m bikes sold each year, the Wisconsin company has elevated the program with a state-of-the-art paint studio and an impressively quick delivery.
BikeRadar visited Trek's operations in Waterloo and Whitewater, Wisconsin, for a close look.
Cut from the cloth
A signature bike can be built from scratch and sent out in about 20 days, Trek claims.
The Project One bikes are handmade in Waterloo, each from dozens of pieces of digitally cut carbon-fiber cloth. Like most carbon manufacturers, Trek uses a combination of unilateral and weave carbon fiber. 12K and 3K carbon, for example, refers to a weave where 12,000 and 3,000 strings of carbon are aligned in each main strand. The strands are about a 0.25in wide and 0.005in thick.
Frames are created in parts, with the dozens of pieces of carbon cloth laid into metal molds, which are then pressurized internally and subjected to high heat to melt and 'cure' the epoxy embedded in the cloth.

Each piece of carbon is digitally cut and hand laid into molds
Although Trek is guarded about its exact assembly process, the company says a Madone frame has about 180 parts, each the result of careful engineering calculations. The longer Trek has worked in carbon, the trickier it becomes to refine the designs.
"Back in 1990, it was easy to carve out weight," said Jim Colegrove, Trek's senior composites engineer. "Just move over to carbon [from aluminum] and make some basic changes." A steel Trek frame at the time, for example, was about 4.5lb, an aluminum frame 3.5lb, and a carbon version, the 5500 OCLV, 2.5lb. "Now the game is so specific. Each layer of carbon is carefully considered."
Similarly, the molds used have become increasingly complex. "We used to have four pieces for the headtube junction lug," Colegrove said. "Now there are between 50 and 60 pieces."
All Trek's molds are designed and produced in Trek's 'old red barn' — the original drafty Trek facility that sits right next to some railroad tracks.

This stay mold assembly is one of the simplest Trek uses — and the only one we could photograph
Painted to suit — by robot
When Trek was building thousands of bikes in Wisconsin, painting was done in huge factory lines. Now that the majority of Trek's bike construction has been outsourced to Asia, the paint program has evolved.
Bob Seibel, the managing paint engineer and a 24-year Trek employee, has overseen Trek's transition from old-school paint booths with a hanging line that resembled mechanized meathooks to the new-school, robotic paint machinery. To create crisp lines between colors on the frame, precision masking is key. That, too, is digitized.

As with the carbon frame pieces, the masking for paint is digitally cut for speed and repeatability
"In the old days we would buy masks from people," Seibel said. "When we purchased Klein, we got custom CAD cutter. Now we can print, cut and laminate our masks within hours of designing them."
There are some neat features of the massive paint line, including an electric oven for drying decals, an RF system for reading ID tags that travel with each frame and the 40,000rpm, 60k-volt atomizer that spreads a nice, uniform coat of paint across a frame.
"In the old shop, we had seven guys," Seibel said. "They had good days, they had bad days, some frames were slightly heavier, some slightly lighter. Now it is an exact science, and there is very little waste."

A robotic arm works its way around the frame, misting atomized paint as it goes
Project One paint can weigh as little as 5g, Seibel said, compared to a standard 28g or so for a regular frame.
White, when used, is always the last coat to go on.
Built to spec — by hand and machine
Once the frames are painted, Trek whisks them down to its Whitewater factory where Project One assembly shares the building with Bontrager's wheel assembly lines. This cavernous building used to house much of Trek's frame construction operation, employing about 600 people, before that was outsourced. As recently as two years ago, Trek still built some aluminum frames here.
Today there are about 20 people working in Whitewater. Trek employs about 800 at its headquarters in Waterloo, approximately 30 in Madison, and another 1,000 around the world.

Every frame travels through assembly with its unique spec sheet on a yellow board
So why scatter Wisconsin employees across three counties? In two words: labor and taxes. "We you go one county over you get tax incentives, plus you get a bigger labor pool," said Bontrager marketing director Michael Browne.
Each Project One frame travels with its unique spec sheet. In the back of the building, towering shelving houses all manner of high-end parts. Here, man, woman and machine work in tandem to pick parts, transport frames down the line and quickly assemble the final product before a quality-control check and careful packing.
It's a different process than Trek used to employ here, when rapid assembly of identical bikes was the order of the day. But with custom orders on the rise — and mass production in Asia for the foreseeable future — Project One's one-by-one creation method remains a point of pride for Trek.
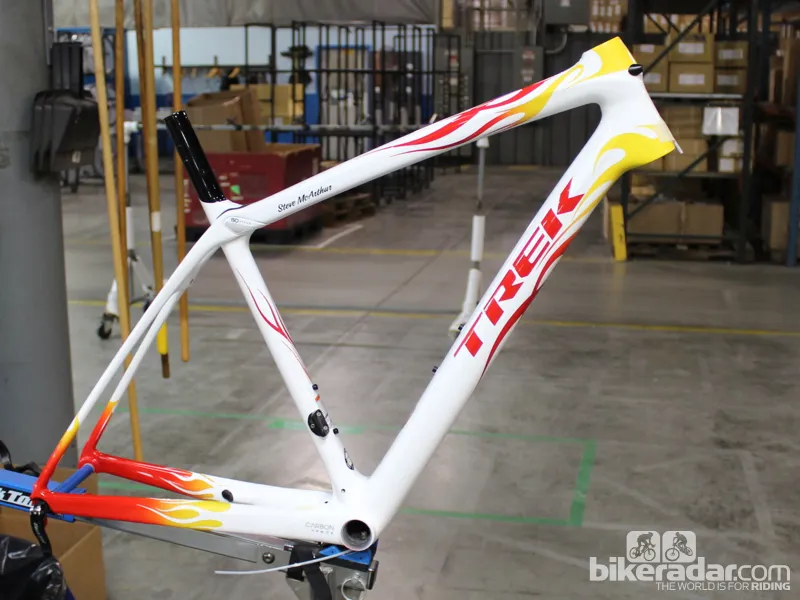
Want your name under the clearcoat? No problem