The UK bike market is currently enjoying something of a boom, with various niche brands having gained a solid foothold on the market. But it's still rare to be able to buy components from a company that not only designs but also manufactures in the UK.
Hope Technology fit the bill, and are going from strength to strength; their parts are now found in bike shop bling cabinets the world over as well as adorning the bikes of pros and ordinary folk alike. There can't be many British cyclists who aren't able to recognise the distinctive green and white livery on sight.
We went along to Hope's new factory in Barnoldswick, Lancashire to have a look at the process which takes parts all the way from initial conception, design and testing, through manufacture, to assembly and eventually despatch to dealers worldwide.
Welcome to Barlick
Hope haven't moved far to get here. The new Hope Mill (formerly a printer's) is just around the corner from their old facility so everything, from staff to machinery and furniture, has been moved across. The company employs around 90 local engineers, machine operatives and admin staff, most of whom live within walking distance of the factory.

Hope have taken advantage of the previous owner's immaculate outfitting of the building and turned the renovated double-height engine room at the front of the mill into a showcase for their products. Photos from some of the best cycling photographers in the business line the walls, viral video hits featuring Hope-supported riders play on the flatscreen TV wall and upstairs there's another gallery featuring all the staff.
Co-owner Ian Weatherill is justifiably proud of the support and affection the town has for the Hope brand and the new factory has a social club, complete with bar, pool table and proper coffee, as well as plans for a local Hope-built trail, making the most of the company's sense of community.

Upstairs there are a handful of bikes on display in the swanky new entrance lobby, from cross country and downhill race bikes to the fleet of liveried-up Hope road bikes. Barnoldswick is in the thick of Lancashire's road tradition and should you see the distinctive kit out and about on the Pennine tarmac, cast a keen eye over the drivetrain. Several riders are currently test riding a 1x10 setup, complete with chain device, which they say gives enough gear spread to tackle every hill they can think of - and those who've rubbed shoulders with the boys in green and white at sportives like the Etape du Dales will know they're handy enough.
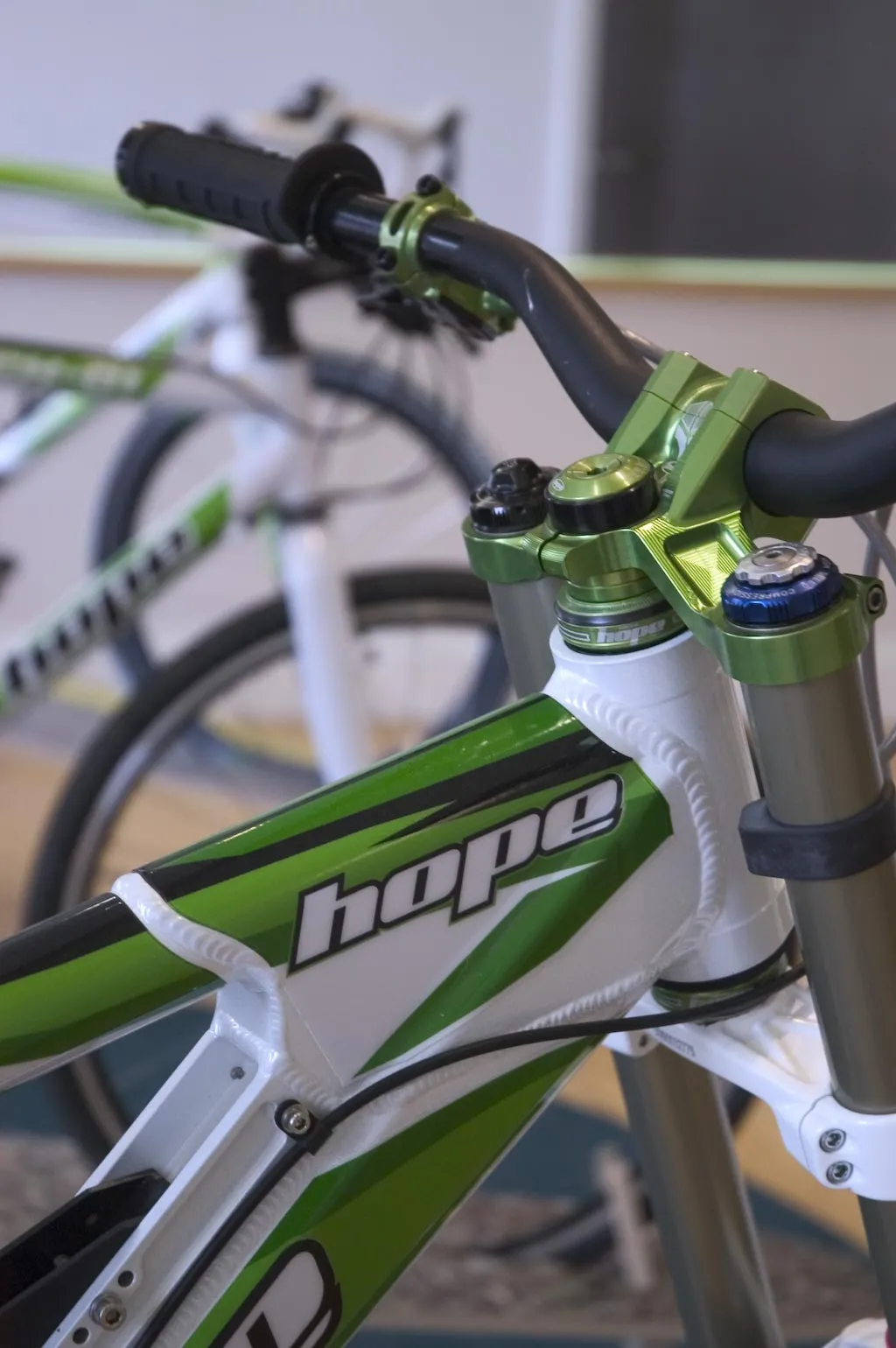

Hope actively support a selection of teams, ventures and individuals across a diverse number of disciplines, from local boy Guy Martin who trains on a Hope-equipped Orange, to caving expeditions, their local trail centre Gisburn Forest and the new Scott Contessa women's UK race team. Many of the staff are riders and racers too, whether road, mountain bike, 'cross or all three. There's a big roomful of staff bikes at the back of the factory that reflects the breadth of cycling culture ingrained in the company.

Palatial as they are, the offices are dwarfed by the scale of the manufacturing facility next door. As much of Hope's production as possible occurs in-house, with out-sourcing only occurring with parts that aren't practical to make at Barnoldswick (eg. carbon fibre lever blades or the electronic components in Hope's Vision lights). Millions of pounds' worth of milling and turning equipment cover the factory floor, running 24 hours a day to attain maximum efficiency.
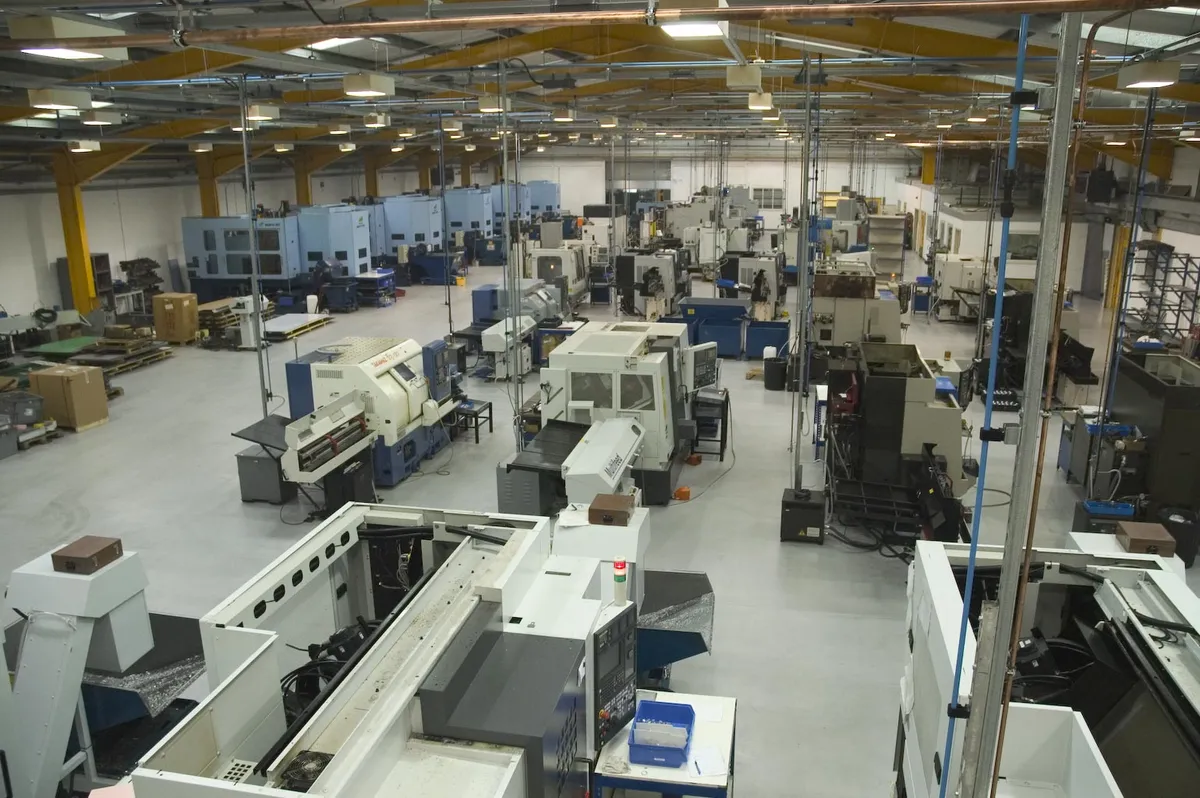

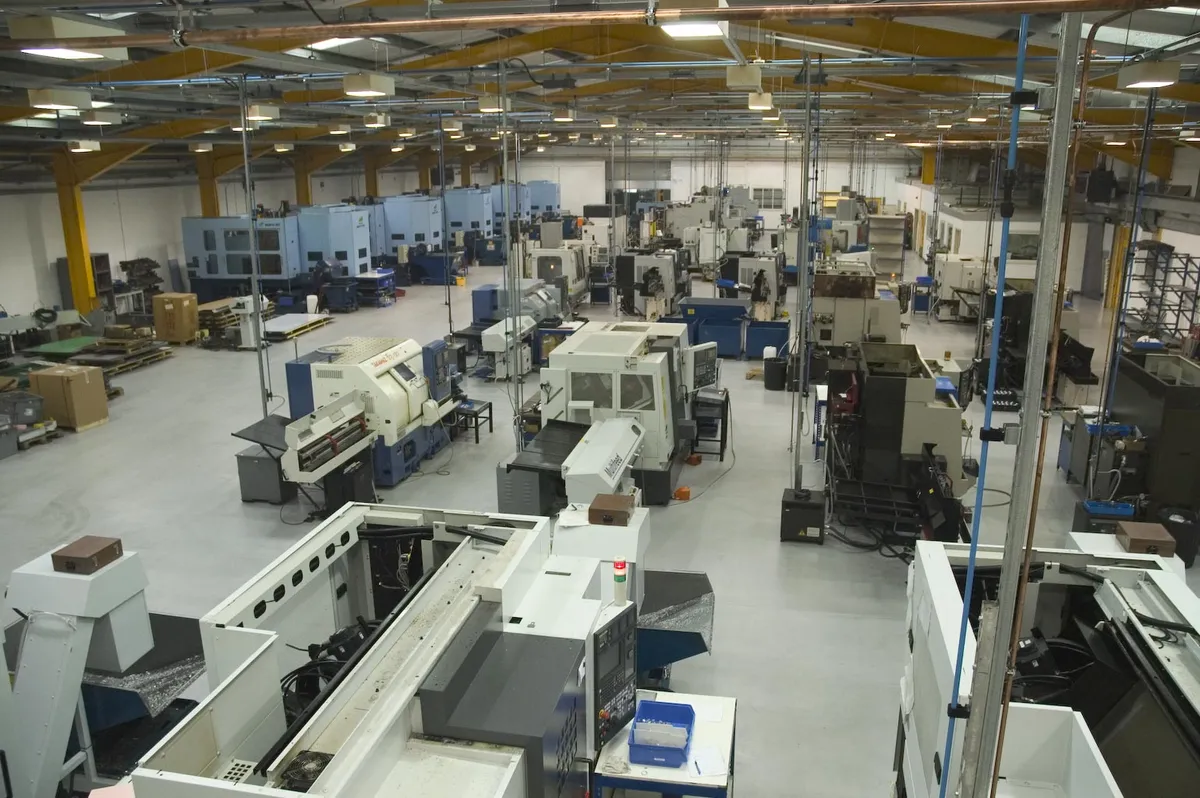

Design and engineering
Hope's design and engineering work happens in house, too. While the corridor of offices adjacent to the factory looks more like a hotel than a design facility thanks to the previous occupier's 'quirky' taste in lighting, it's given Hope plenty of room for the desk-based parts of the company to get down to business.

With a 3D printer buzzing away in the corner and various intriguing 'paperweights' floating around on desks, it's an interesting place for the nosey

Three-dimensional nylon printing allows for quick and accurate models. The next step is printed titanium. Rather more expensive, we suspect...

Integrated freehub and cassette: allows a much smaller sprocket at the high end of the range, making properly useful 1x10 a real possibility.

Want discs on your 'cross or road bike? Then you'll be interested in this: it's a work-in-progress design for an STI lever>hydraulic disc brake converter, designed to be mounted neatly beneath the stem

Perks of the job: want a new flat pedal? Make yourself one

Not your usual cassette body

This is Hope's new chainset and single ring chain device. A version of the 1x10 drivetrain is undergoing testing on a few staff bikes. Including the road ones...
Testing
Like everything else, Hope do their testing and quality control in-house. The test room is a satisfying mix of scarily heavy-looking machinery and Heath Robinson-esque setups.


This dyno is for brake testing, used to simulate pretty much every riding condition you can think of

It gives access to everything from speed to temperature for on-screen analysis and refinement

A throttle-controlled keyboard? Perfect for lacklustre Mondays
Warranty

Hope's after-sales service is legendary and the warranty room gives a new meaning to desk-driving

All Hope's return and repair work is done in house and they keep spares going back as far as is practical. Which is often a very long way indeed
Goods in

It might not look glamorous but this is where the magic starts

Manufacture from scratch requires large amounts of raw material and everything from standard stock product...

...to extrusions custom-made for specific parts arrive here

Forecasting demand and buying in appropriate stock of raw materials by the tonne up to a year in advance is all part of a day's work here. Scary

This is also where the off-cuts end up; manufacture creates inevitable waste and while it's minimised by efficient production, there's still plenty to dispose of

All the swarf, spare bits and mistakes are sent off to be recycled: it's good environmental and financial sense
Hubs

This is how a hub starts, as part of a large box of raw aluminium blanks that arrive ready to be converted into shiny moving parts

State-of-the-art CNC machines run 24 hours a day

Though the milling and turning machines still need human intervention to load and operate, they allow Hope to run a massively efficient factory floor with the minimum of downtime

There's still room for traditional tools, though...

Quality control happens all the way through the process, not just at the end. Here a machined hub shell's being checked to make sure that the bearings will fit perfectly, with tolerances down to thousandths of an inch

Well-used and beautiful tools to go with the finely honed skills

The machines might be automated but they still need to be given a gentle prod every now and then...

Just a reminder – on the neighbouring machine, the blanks are loaded the other way up

CNC machining in action. Looks like numbers to us but we were assured that it was busy making hubs...

Tooled up

Don't put your fingers in here

More machining. It's a dark and mysterious business

This is the EDM (electrical discharge machining) machine, busy cutting freehub pawls from sheet steel

The process uses an electrically-charged wire to slice through material and can cut tiny, complicated items precisely
Rotors

Rotors are cut from sheet steel by a plasma cutter – spectacular and speedy

Don't put your fingers in here, either

Careful pattern layout minimises waste...

...all of which is sent off to be recycled

Stacks of ready-to-cook rotors appear as if by magic

Once cut, the rotors are cooked to temper the steel, then cooled evenly in a press to keep them flat before assembly

Even the most esoteric of standards still find some love here

if you've attended a race event that Hope support, you'll probably have seen these before: yes, even their customised trophies are made in Lancashire
Waste not

It might be low-tech in comparison to the computer-controlled machinery around it but the thread rolling machine that sits unassumingly on the shop floor is just as efficient

It threads a skewer in a second and is worked by the same operators who load and watch the CNC machines

Efficient, practical, and very Hope
Finishing and anodising

Before anodising can happen, the finished machined parts are polished


Larger components are racked while small parts go straight into the tubs which are filled with various polishing compounds

Eco-friendly ground walnut shells do the fine stuff, whilst ceramic beads of varying sizes remove rougher edges

Anodising happens in-house, too. Polished parts are racked by hand

Then they're primed with an electrical charge before being immersed in a series of temperature-controlled baths of dye

This is one anodising line; once the move's complete there will be three but to avoid any interruption in production Hope simply built a new one in the new factory. Logos are laser-etched into the anodised parts before they move on to assembly
Hope Vision

Quite a few of the components needed for Hope's Vision lights are bought in but they're still assembled and tested in-house

The soft harnesses which adapt the lights for use as a regular head torch are made by machinists here, too

You'll find the distinctive Hope livery everywhere from UK fell races and mountain marathons to the deepest South American cave expeditions
Hoops

Hope's wheels are deservedly popular and they're all built in-house, too

Rims, spokes and nipples are bought in in quantity to produce everything from heavy-duty downhill use to deep section carbon tubs for the 'cross brigade

They're available in all the combinations you can think of and probably more besides

Rims are laced to hubs by hand, then taped and tensioned by machine
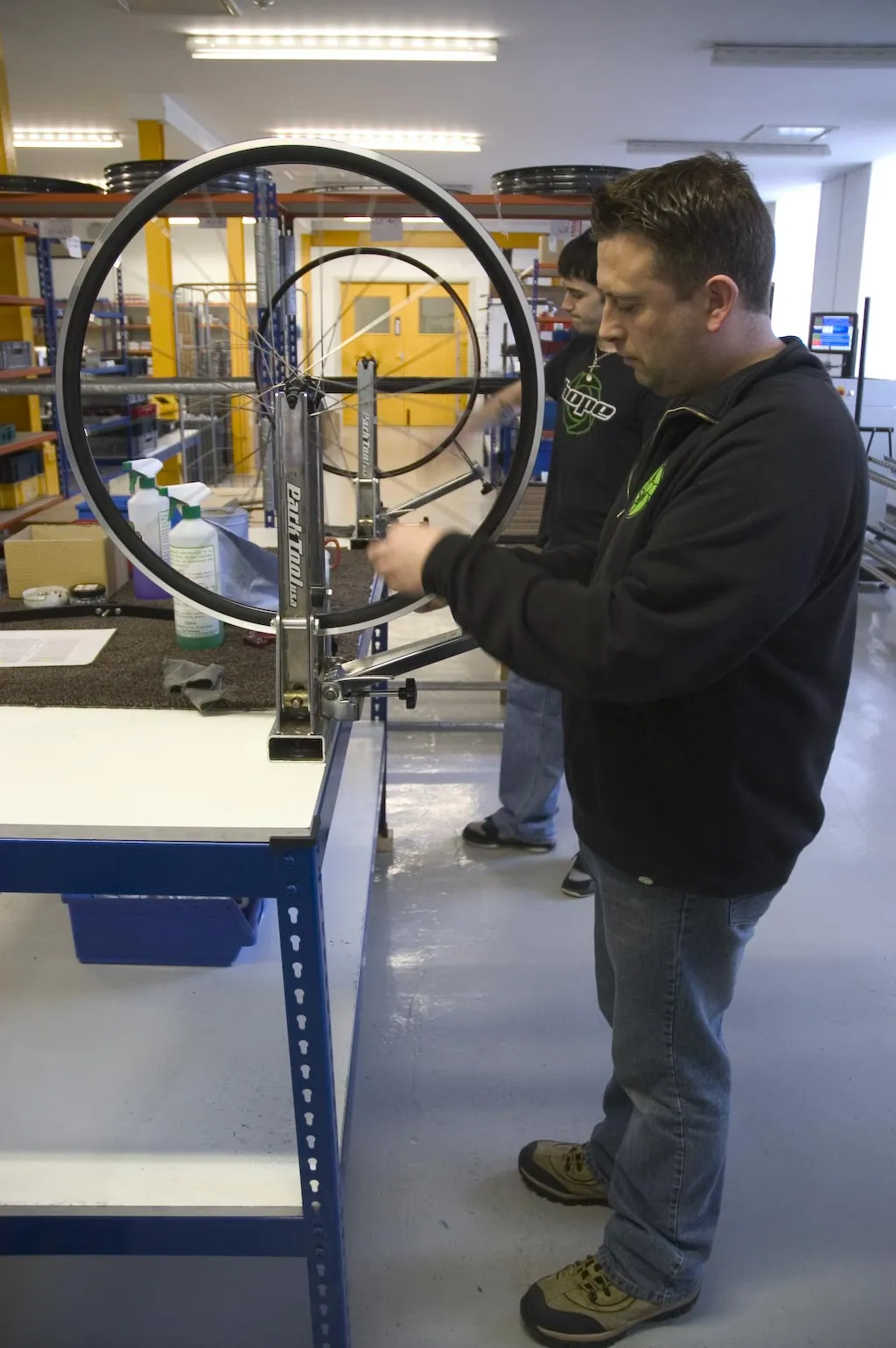
They're then hand-finished, stickered and boxed ready for despatch
Assembly

This is where all the manufacturing sweat comes to fruition. Parts are gathered and put together. Everything from assembling a hub...

...to compiling the various parts of headset is done here

Parts are racked up when they're ready to go: these are finished brake levers waiting to be attached to their hoses and callipers

Assembled brakes are filled and bled using a pressurised tank of fluid, custom made for the purpose of quick and easy bleeding. Vital when you're doing hundreds of brakes at a time

Finished parts are boxed and racked. If you're thinking that doesn't look like much storage, you'd be right; Hope have efficient, just-in-time manufacture down to a fine art

Right at the end of the line is the target: a very big pile of boxes, all ready for despatch to dealers by courier
For a further look behind the scenes at Hope, check out the video below by MTBcut:
Unable to load media