Remember those yellow wooden pencils you wrote with as a kid? The graphite in those pencils could soon revolutionise the way we think about composites. Graphene, a related new material, could be used to make a durable 400g frame — and charge your head unit and electronic drivetrain.
Still in its infancy, graphene is creating quite a stir for its strength-to-weight ratio, in addition to its electrical and heat conductivity. Derived from graphite, this one-carbon-atom thick material was the subject of the 2010 Nobel Prize winning paper in physics, which claimed a one metre-squared sheet of graphene weighing 0.77mg could support a four-kilo cat without breaking. (No word on dog compatibility.)
The same paper also states that this material could be woven into fibre and utilised in a similar manner to carbon fibre, meaning in the not too distant future you may be riding a super light, super strong bicycle made of graphene composite.
Spanish helmet brand Catlike, and Austrian ski manufacturer Head are both claiming to already be using graphene. Vittoria also says it uses graphene to reinforce its new carbon fibre road rims. Patrick Varas, a product manager at Apollo Bikes, the Australian Catlike distributor said, “In the Mixino we are using aramid as well as graphene nanofibres in the reinforcing roll cage. Graphene is much stronger and lighter than the polycarbonate roll cages used in previous helmets, and helps to keep the helmet together in case of an impact."
Trevor Brown, the CEO of Rosbert International Pty Limited, the Australian distributor of Head Skis echoed similar information in an email to BikeRadar: “Graphene is a stronger and lighter material and Head has a patent for 10 years on using this technology in their skis. They are graphene sheets which go all the way along the length of the ski.”
With applications in everything from smartphone screens to satellites, graphene seems be the next super material.
What is Graphene?

Graphene could change the way we think about composites
Discovered by Professor Andre K. Geim and Professor Konstantin S. Novoselov, researchers at Manchester University, graphene is a two-dimensional single layer of carbon atoms. Carbon itself exists in many forms. However, the most common is graphite, consisting of multiple layers of stacked carbon molecules with a hexagonal atomic structure resembling chicken wire.
Graphene-like structures were discovered back in the 1960’s but researchers were unable to isolate a flat one-atom-thick layer of the material. It was not until 2004 that researchers at Manchester University were able to isolate a single 2D layer of graphite. Oddly enough, according to their paper published in Science, the researchers used Scotch tape to exfoliate layers of graphite until they had a one-atom-thick layer.
The discovery of graphene proved to be groundbreaking, not only for its electrical conductivity, but also its strength and impact resistance.
“They are saying that this stuff is so strong and light, you could build a space elevator," Raoul Luescher a carbon expert, and the director at Luescher Teknik told BikeRadar. "So instead of sending a rocket up to the International Space Station, you could just have a cable of this stuff, hook things onto it, and send them up on the cable.”
“There is also an application in ballistics protection for the police and the military. They are saying it’s much better that Kevlar, Spectra and all these others materials because of its damage tolerance and protection," Luescher said. "The problem is, to do this they need multiple layers, and they don’t know how to do that on a production scale yet.”

The high tech tool the researchers at Manchester University used to isolate graphene
Darren Baum, founder and head frame builder at Baum Bicycles highlighted graphene’s potential for medical use. “I think it is going to be one of these materials that will play in our everyday life before it impacts us in the bike world," Baum told BikeRadar. "I think we will see it used for repairing joints, broken bones and all the wonderful stuff they come up with in that sense.”
What About Carbon Nanotubes?

Nanotubes are used to reinforce the epoxy resin in some carbon fibre frames and components
Already widely used in the cycling industry, and something that dates back some time in composites are carbon nanotubes — three-dimensional rolled graphene sheets. Designed to reinforce composites, carbon nanotubes fill the gaps between sheets of carbon fibre, which therefore requires less of the weakest component - the epoxy resin.
Dave Musgrove, the product engineer at Sydney based Cell Bikes, wrote his honors thesis on 'Carbon-nanotube-reinforced epoxy resin, and nanocomposites for use in carbon fibre composites'. “In normal carbon fibre you have all your fibres which are packed as closely as possible, with epoxy resin between the fibres," he said. "You want to squeeze as much resin out as possible because it’s adding weight and not much strength. So the idea is in those gaps, because the resin is weaker than the carbon, cracks can propagate pretty quickly.
“With nanotube reinforcement, rather than traveling for hundreds of nanometers through the resin before the crack hits a carbon fibre, it hardly goes anywhere and hits a nanotube. Because that carbon nanotube is really long and joined to a lot of epoxy it either has to break — but nanotubes are very strong — or it has to pull out of the resin. So there is more of a reinforcement at the nano-scale that helps with fracture toughness.”
While many bike brands like BMC, Pinarello, BH and Catlike (we suspect by ‘graphene nanofibre reinforcement’ they are referring to carbon nanotubes) are claiming to utilise nanotube technology, not everyone is convinced they are anything more than marketing jargon.
“The engineering manager here (at Enve Composites) tried using nanotubes, but didn’t find any real benefits. The hard part was to find anyone that was getting in any samples that we could test to validate the claims. Easton and a few other bike companies have tried to work with nanotubes, but haven’t really done anything effective,” said Carl Turner, a design engineer at Enve Composites.
More optimistic about the benefits of carbon nanotubes, Musgrove warns it’s not as simple as just painting nanotubes on, “It’s some pretty full-on procedure just to mix the nanotubes into the epoxy, and make sure they are not clumped or curled. It’s not like a carbon factory can be like ‘sweet we are going to use these nanotubes’ and chuck them into the process. It requires a whole new set of procedures. I think for a few companies that are using nanotubes, it has been kind of a buzz word in the cycling industry.”
Why Graphene?

At the moment manufacturing large quantities of graphene seems to be a problem
While only slightly differing from carbon nanotubes, graphene is a 2D flat sheet. The carbon atoms that make up graphene sheets are connected by strong covalent bonds, and as Musgrove explains they are looking to share electrons.
“On the edges of these sheets, the carbon atoms are only connected to two other carbon atoms, and are looking for another pair. In the center of the sheet they are joined to three carbon atoms. So this means on the edge of each sheet there are spare electrons that are really reactive. Theoretically the bond with the graphene sheets would be really strong, and would not want to pull out.
“The other aspect is because there are two sides of a normal graphene sheet, each individual carbon atom has a few spare electrons, and each side is really reactive. It is looking to stick, not only on the edges but also on both sides; so there is potential to bond really well with other materials.”
Despite their similarities in chemical makeup and properties, graphene is better at contributing its mechanical characteristics to the material it’s mixed with. Because a polymer cannot penetrate the middle of a nanotube (as it is too small) the bond is not as strong. With more surface area to bond with, the carbon atoms in graphene can create stronger bonds than nanotubes, becoming better utilised in the composite.
With a tensile strength of 130 gigapascals (Gpa), graphene is claimed to be the strongest known material in the world, 2000 percent stronger the toughest (Toray T1000) carbon fibre (6.3 GPa) and roughly 46 percent stronger than diamond (the precise tensile strength of diamond is unknown, however the strongest ever recorded is 60GPa).
High-strength materials are attractive, but another key factor is bending modulus. Take ceramic; a material with high tensile strength but a low bending modulus, or in other words ‘brittle’. This is easily demonstrated when you drop a ceramic bowl: it shatters into a million pieces instead of bouncing.
“If you hold a material at a certain point and push down on it measuring the way it flexes and the stiffness, you’re measuring a combination of tension and compression," said Musgrove. "One side is being compressed while the other is being pulled apart — this is bending modulus."
“If we go back to carbon fibres, you can get super high modulus carbon fibres. However, they don’t have as much strength. If you load that high modulus T1000 carbon it will not flex much, but if you give it a real sudden yank it just breaks because it has a low bending modulus."
So not only is graphene super strong, it is also not brittle like hi-modulus carbon fibers. Theoretically this means that a graphene composite has the ability to absorb a sudden impact, say from a crash much better than current materials. The problem is, to create a composite, thread needs to be woven into a usable material.
“Theoretically if someone has been able to weave it (graphene) in with carbon, once you have one strand of this stuff that is effectively using graphene’s properties, then you can make what you want with it,” explained Musgrove.
Such fibres do exist but they are mostly experimental — neither Head, Catlike, nor Vittoria delves into the specific details of their use of graphene.
Application in Bicycles
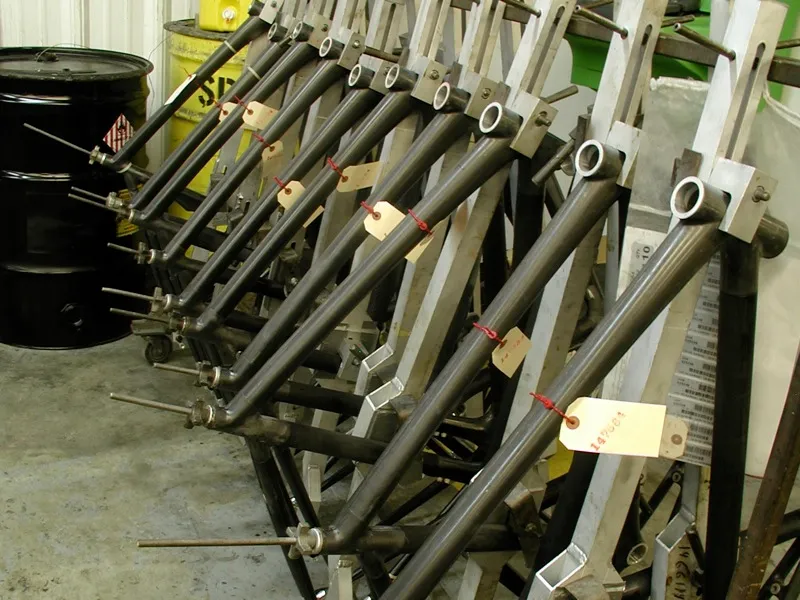
Will your next frame be made from graphene? It's unlikely to be honest...
The most obvious application for a composite material like graphene is in frames, wheels and other components currently made from carbon fibre. As Musgrove explains, “Frames are becoming extremely lightweight, and there is not a lot of weight to be shed in the current crop of high-end frames, many of which come with maximum rider weight limits. With graphene, you could take that sub 700g frame, produce it without a rider weight limit and confidently offer a lifetime warranty or even possibly go lighter. There is a potential for it, but I reckon it will come at a substantial cost.”
While graphene is still in its formative years, the high strength, low weight and bondability could make graphene an ideal composite material. Despite these mechanical characteristics, it’s graphene’s other properties that create the most exciting possibilities.
Carbon clinchers have been plagued with horror stories of catastrophic wheel failure caused by resin overheating, resulting in the tyre bead folding out like a wet taco.
“Another thing that graphene could be used for is heat dissipation. With (carbon) clinchers you have that brake pressure from the calipers. That resistance generates a lot of heat, and the epoxy starts to degrade. Graphene may be a way you could move the heat away from the brake track,” Turner said.
Let’s not forget that graphene is also a phenomenal electrical conductor. With recreational cyclist running electronic drivetrains, power meters, computers, lights, and in some cases motors, there is an increasing dependence on batteries. While friction and hub based generators have been around for quite some time, graphene could potentially allow for a different power source.
“I am being pie in the sky here, but a graphene frame could potentially be a super-capacitor which gets charged by a solar panel somewhere on the bike, constantly keeping your Di2 and lights charged,” said Luescher.
Still A Ways To Go

Developments in graphene have allowed researchers to create graphene oxide fibres
While these are all exciting prospects it is likely to be sometime before we see a mass application of graphene in bicycles. To this point the work done with graphene is mostly lab based. Both Musgrove and Luescher stressed that making a small bit of material in an R&D lab, versus producing it in a commercial capacity, are two completely different things.
On the other hand Baum is unsure the cycling industry is quite ready to move onto the next big thing in composites.
“I think we are still trying to understand the bike more. To take the next big leap forward in bike technology I think we need to understand what we are really looking for,” Baum said.
This sentiment is echoed by Turner who believes we still have a lot of improvements to make with carbon fibre. “I have seen what we can do with just standard carbon technology, and being able to improve our process, we get better results out of it. Carbon fibre is only 40 or 50 years old, and we are still pushing its limits and finding out what we can do with it.”
Baum also pointed out that even if someone does figure out a way to produce graphene on a large scale, if other technologies are not to the same standard the benefits might be lost.
“Tensile strength is a fantastic thing but it comes back to what resin it can work with, and if they don’t have the same tensile strength internally it creates a very weak joint. Not the head tube joining the down tube, but internally within the resin you may get something delaminating.
“There are people that put Kevlar in their frames, and it is very good for impact strength. But, at the end of the day the resins are not good enough. When it all stretches, it all stretches the same; so the resin technology becomes extremely important,” Baum explained.
Final Thoughts

The 2010 nobel prize winning paper in physics stated graphene could be utilised like current carbon fibres in composites
It was only in 2013, researchers at Rice University were able to produce a graphene oxide fibre that is super strong, and capable of being woven into a carbon composite. A year later a collaboration between Shinshu University in Japan and Penn State in the USA led to a scalable method to produce a similar graphene oxide yarn.
Even more recent in November, 2014, the Korea Electrotechnology Research Institute (KERI) has demonstrated new technique using 3D printing to produce straight graphene oxide nanowires as well as woven structures.
It will likely be some time before we see graphene take a hold of the cycling industry, if ever. Even as this story is being written, breakthroughs are being made in the field of graphene. The problem at the moment seems to be producing the material on a mass scale large enough to support a commercial investment.
“I tell people my grandmother was born before the Wright brothers first flew, and then saw a man go to the moon before she died. It is pretty incredible how quickly things happen and the changes we are seeing with materials at the moment is pretty interesting,” said Luescher.
“It’s more likely to be in golf clubs or tennis racquets before bicycle frames. These are simple parts to make with a simple shape, and if they do fail, people aren’t likely to die,” Luescher said with a laugh.
Before sporting equipment, it is likely that we will see graphene utilised by the military and in the biomedical field. Nonetheless, graphene offers an exciting prospect and will likely have an effect on our daily lives in the not too distant future.