Charge Bikes has developed a cult following among urban, cyclocross and mountain bike riders, thanks to its clean, stylish designs. Now, Charge founder Nick Larsen has developed a new brand called Fabric, in collaboration with aerospace giant Airbus, which will produce saddles with 3D-printed titanium rails and whisper-thin carbon shells. Fabric will create saddles for bike brands such as Cannondale, Larsen said.
One of Charge's biggest successes has been its line of saddles. With the Scoop, Spoon and Knife, Charge created a popular range of affordable saddles, selling more than a quarter of a million units, according to the company. With Fabric, Larsen can expand even more.
"We saw a need for a bigger and better saddle range, as over the years we've had plenty of bike brands wanting to spec our saddles on their bikes," Larsen told BikeRadar. "I thought it was a little strange for a saddle that's come from a bicycle brand to end up being fitted on competitors' bikes. So the genesis of branching out into a parts and accessories line seemed obvious."
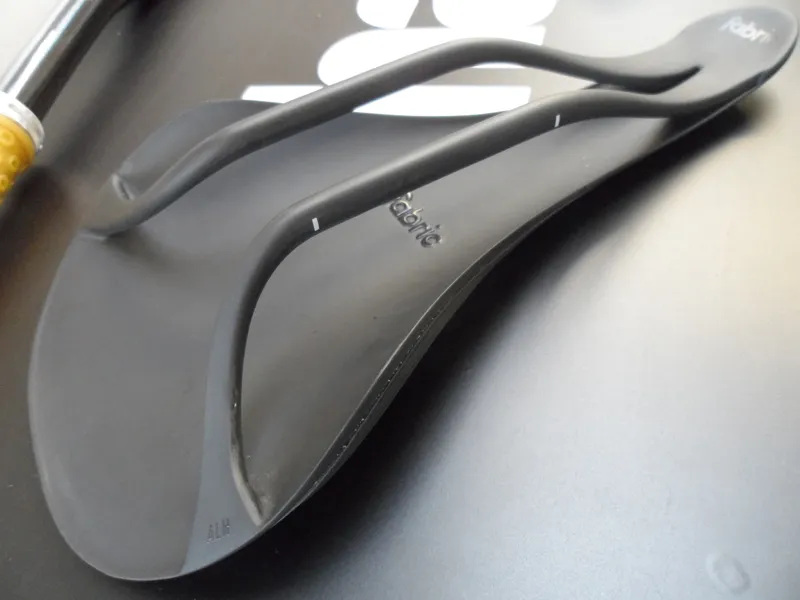
A prototype Fabric ALM saddle uses an entirely new rail-to-shell construction method
Creating a new brand gave Larsen the opportunity to completely overhaul not only saddle design but how the saddles are actually made.
"There are plenty of excellent saddles around, from classic designs to the latest carbon lightweight offerings. But there is something that holds back the design of saddles moving forward: the way in which they are manufactured. Globally, there aren't actually many companies producing saddles. Irrespective of materials, they are all made in the traditional way. What we aim to do with Fabric is totally change how we look at construction to really improve them."
To do so, Larsen and his team looked outside the bike industry and have come up with some very interesting new tech for Fabric. Fabric has not yet officially launched, but BikeRadar got an inside look at the technology behind the forthcoming brand.
3D printed rails, sonic bonds and 'hyper-pin' technology
Charge Bikes started using 3D-printing technology on the rear dropouts of its titanium cyclocross frames, working in partnership with Airbus. So when when looking at creating the rails for Fabric's flagship ALM (additive layer manufacturing) saddle, Larsen went back to Airbus. The hollow rail is shaped to act as a leaf-spring, with wall thicknesses of just 1mm, except for at the reinforced clamp section. The design weighs a third of the ti rails on the Charge knife saddle.

Charge is 3D printing titanium rails with tiny pins that interlock into the saddle's shell
Traditionally, saddle makers use glue and/or bolts to attach rails to a saddle's base. With Fabric, there is another Airbus technology: the 'hyper-pin' connection. Where a standard saddle would have rails inserted into the shell, Fabric uses a series of 3D-printed pins that interlock into the shell. These are then sonically bonded to the carbon shell, which is only 1mm thick. This method of construction is used by Airbus in some of its aeronautical applications, Larsen said, so that with just eight pins interlocked, the saddle junction is able to withstand a whopping two tons of force.
3D-printed titanium rails in this design is an expensive business, which means the ALM Titanium saddle will be at the top end price-wise. But Fabric and Airbus have already worked on a cheaper carbon alternative using the same leaf-spring design. The near-final prototype of the carbon ALM saddle we saw tips the scales at just 120g, hugely impressive for a saddle that still retains real padding as opposed to the usual ultra-light unpadded carbon designs.

The rail/shell junction at the nose, with one of two rails in place
"Airbus must take the credit for the carbon technology within the saddles," Larsen said. "It's something we just haven't seen in bikes ever. We've tested the rails and base and they've been bent under testing to 90 degrees and still didn't fail. That should mean the Fabric saddle should take the worst of impacts and still be fine to use."
Speaking of fabric, the Fabric uppers are attached in a very clean-looking manner. Instead of the traditional hand-applied method, where the cover is wrapped around the base and tacked and/or glued onto the base, Fabric sonically bonds the upper on. The difference is striking.
Three, it's the magic number
Alongside the ALM design, Fabric also created a whole line of saddles for a range of widths in both the sit bones and the wallet. The range is based around three designs, each with three width options and three different rail materials.
Fabric based the designs on body type, irrespective of gender and rider position. The Line range is for the narrow hipped (read slim) while the Scoop is for the average body shape. The Cell is for the wider hipped and stockily built.

Other Fabric saddles use a more traditional method of rail-to-shell assembly
From there, you then choose the shape: a flat profile for an aero position, a shallow shape for a moderate position with the back at 45 degrees to the ground, and a radius shape for more upright riders.
There are three types of rails: chromoly, titanium and carbon. Finally, there are two types of base: carbon (expensive) and nylon (more affordable).
The Cell saddle has a trick up its sleeve. Fabric wanted the comfort afforded by a gel saddle but without the weight penalty. So again Fabric looked outside the bike industry, and partnered with a major sportshoe manufacturer to use the same technology as air-filled running shoe soles. The Cell's translucent air-filled padded upper is bonded to the base. It's highly tactile and different from anything on the market and substantially lighter than gel offerings.
BikeRadar has a few sample Fabric saddles on test now, so we'll report back soon on their performance.

Expect a full report on how this Fabric saddle performs soon