The mass manufacture of bicycles in the UK has almost been consigned to history. But in one corner of west London, Britain’s biggest bike builder has recently upped capacity to cope with demand. Welcome to the fold…
Popping up into the London sunshine at Notting Hill Gate tube station, with Brompton’s global brand manager Ross Hawkins, we unfold our bikes and set off past Kensington Palace through Hyde Park, Mayfair and Soho: destination Covent Garden.
Born in London in 1977, the Brompton bicycle took its name from the Brompton Oratory Catholic church in Kensington
Our bikes are two of the west London firm’s portable wonders, which is why we’ve been able to complete the first part of our journey from Brompton’s Greenford factory under TfL’s steam rather than our own. And that, in microcosm, is the genius of designer Andrew Ritchie’s famous creation.
You’ve almost certainly encountered a Brompton folding bike on a street or railway platform; perhaps you were impressed, perhaps you were intrigued, or perhaps you were aghast at the very idea. Whatever your thoughts, if one of them is that they are nothing more than interesting curiosities beloved of suburban commuters who wouldn’t otherwise be seen on two wheels then you might be surprised to learn that 50,000 of these small, hand-made bikes fly out of the firm’s west London factory every year — a remarkable success story for a business built from one man’s vision.
“I’d played with one or two other ideas before the Brompton,” remembers inventor Ritchie, “and although at the outset with the bike I had nothing else on the boil, I didn’t expect or intend to devote my working life to the project.
“When the original plans came to nought, I realised that the only way forward was to make and sell the bike independently.”
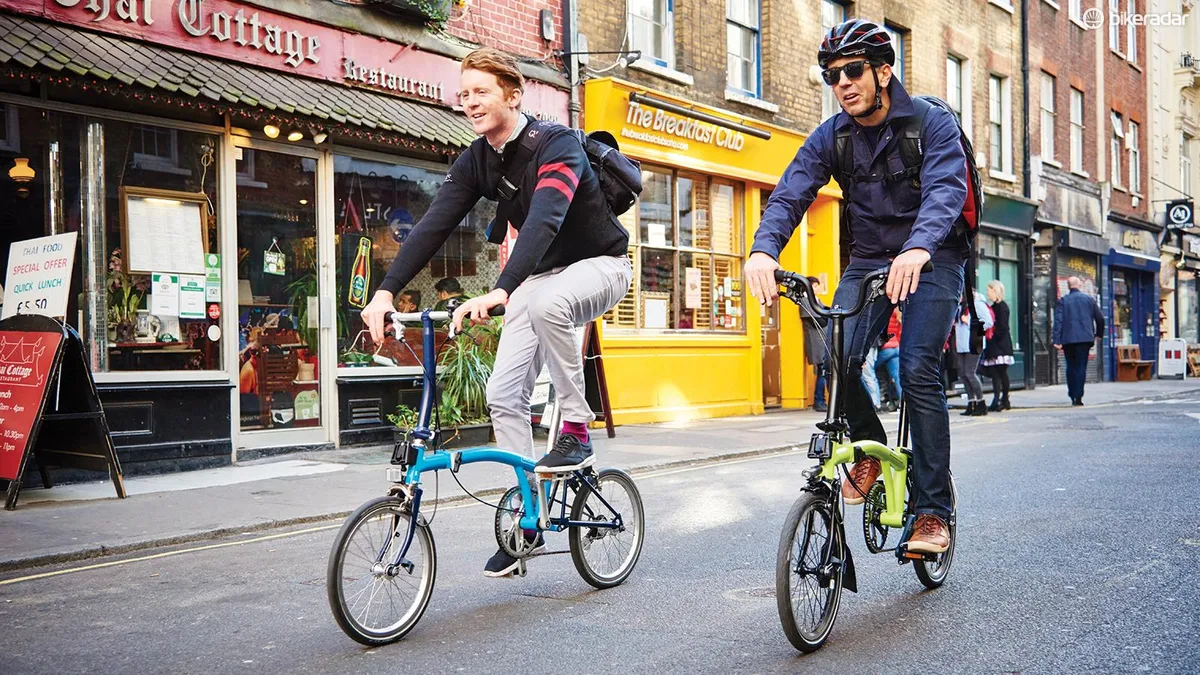
The early days of Brompton
Born in London in 1977, the Brompton bicycle took its name from the Brompton Oratory Catholic church in Kensington, visible from the window of inventor Ritchie’s flat. Folding bikes existed before, but none had the simplicity of design and ease of use that would become the enduring trademark of this British institution.
“Andrew’s father was an investor in Bickerton, one of the first folding bikes,” explains Hawkins as we ride. “As an engineer Andrew thought it was interesting but that he could do better. Inspiration was taken from the Bickerton, and although the modern Brompton looks a lot different what unites them is the rear wheel folding back under the bike.
“Testament to the original Brompton design is the fact it hasn’t changed phenomenally from the first prototypes. Almost every component is different, but the design’s still there, and that’s how it’s achieved its iconic status.”
While Ritchie set about designing a bike, it was never his plan to manufacture: the idea at the time was to license the design to someone such as Raleigh, which was already well established in bicycle manufacturing.
“The response he got was that although the idea was interesting, the manufacturers weren’t convinced there was a market or that the idea was scalable,” says Hawkins.
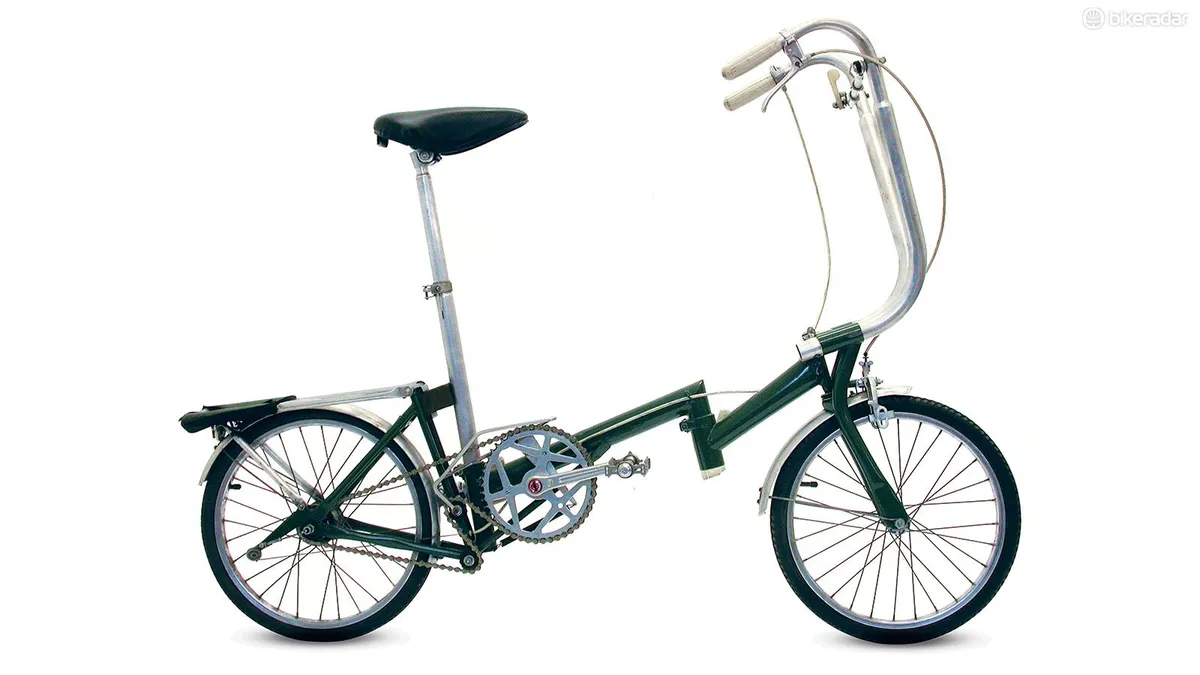
Faced with scepticism that his design could ever be built as more than an occasional one-off, Ritchie did what any clued-up frame builder looking to get a foothold in the industry would do today: he crowdfunded.
We see that these bikes are so much more than ‘assembled’ on site as we’re faced with a line of workers hand-brazing steel tubes
“Andrew took the idea to friends and explained that he needed to prove it was possible to make a hundred of these bikes,” explains Hawkins. “He went out to 100 friends and said that if they bought a bike now he would deliver it to them in six months’ time, and then if the company was successful he would pay them back, so they’d get a free bike.
"The first year he did that was 1980. He made them, delivered them and was able to pay people back by 1993! So it did work, but it took a while.”
Those first prototypes were manufactured by Ritchie on his kitchen table and in a shared industrial unit in Chiswick Park, and the Brompton has been handmade in west London ever since.
“We’re asked why we’re still based in London, rather than Asia,” says Hawkins, “and the first reason is that Andrew didn’t start out because he wanted to build a business and make lots of money, he just thought this could be a useful product.
“He lived in London and thought it would be great for getting around town, being able to take on trains and the tube and things like that. The reason it’s based in west London is that he wanted somewhere he could cycle to from his flat in Kensington, so it started out around Kew and Chiswick and now here.
“All the guys that work here have been trained here: the knowledge is in the staff, and as the business has grown the number of staff with that knowledge has grown as well, so it’s never been the right time to outsource. We now have a brand identity that is based around being made in London, so it becomes a benefit to build here.”
Hand brazed and handmade

In the factory we see that these bikes are so much more than ‘assembled’ on site as we’re faced with a line of workers hand-brazing steel tubes.
“All our brazing areas are set up to do different tasks,” expands Hawkins. “The frame starts at one end and moves along through each of these cells where a different task is being performed.
“Each of these jigs is set up to do different things, so we need one for each part of the operation. This is when you start to realise how much Andrew did in terms of the operation, because back in the 1980s he had to hand-draw engineering drawings. He drew how he wanted the bike to look, and its constituent parts — the mainframe, fork and so on — but then each bit of tooling, each jig, would also require drawings.
"So there are not only hundreds of drawings relating to the bike, there are hundreds relating to the manufacture and tooling. Each of the jigs we use now is either exactly the design Andrew came up with or a variant of that original design. So he didn’t just design a folding bike, he designed an entire manufacturing process.”

Brompton’s brazers are some of the best in the land, all trained on site.
“We take people from welding and non-welding backgrounds,” says Hawkins, “but you can’t typically go out and find brazers: it’s a bit of a dying skill and having enough trained brazers was something that at one time held up production and left us unable to supply enough bikes to meet demand.
“With other areas of the company, if we wanted to double the sales of bikes we could double the number of people working in those areas, but you can’t phone up a recruitment agency and ask for 10 qualified brazers to join the team. We train them ourselves and even if they come with welding experience it can take 18 months to get them to where they are able to work on all of the different parts of the bike.
“Brazing is kind of like high-temperature soldering, rather than welding. This is a simplification but when you weld two pieces of metal together you are heating them up and the ends are forging together, with brazing you’re putting two bits of metal together and introducing a third bit of metal to act as the glue, so you don’t have any movement of the two metals being joined.
“One of the most skilled areas is bottom bracket manufacture, and this uses what we call fillet brazing, producing an almost thumbed effect which makes a really strong joint. The bottom bracket has to be very strong, and to achieve that is a real talent.
“Each of these guys has their own stamp which they put on their work, so if we do have any issues we know who has brazed the various parts of the bike, which gives us quality control throughout. But the guys here won’t need to see that stamp to recognise each other’s work, because like recognising handwriting, they will know who’s brazed certain parts.”
Electric dreams
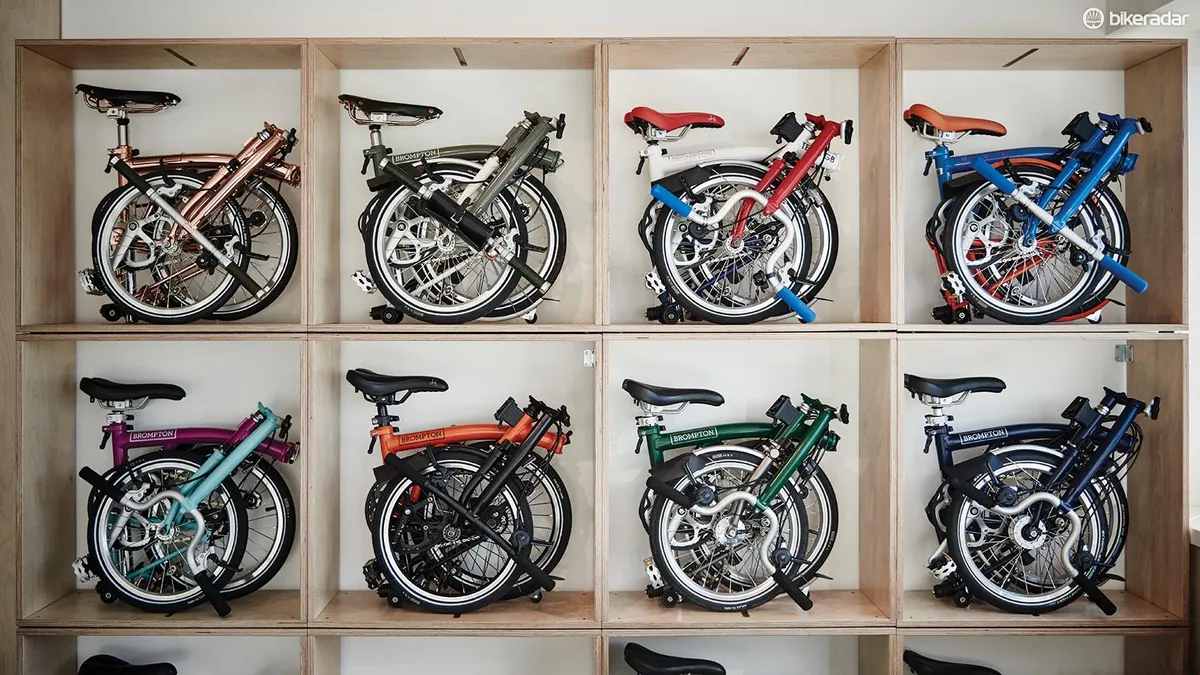
Across the other side of the factory floor is the assembly line, where each bike is built to order (go on the Brompton website and you can spec out your own model). “It’s not always the end user speccing the bike,” adds Hawkins, “sometimes it will be a shop or distributor.”
One significant change is in the offing with the imminent arrival of an electric Brompton
There are a lot of bikes to assemble these days. “From 1988 into the mid-2000s Andrew built Brompton into a good sized business,” explains Hawkins, “making about 10-15,000 bikes, and then in 2007 the current CEO Will Butler-Adams, who joined Brompton as part of the engineering team, led a management buyout. It would be fair to say that the focus up to the mid-2000s, led by Andrew, was all about the bike, and since then we’ve become a bit more outward looking. Will has invested more in sales and marketing and getting the product out there.
“We’re now producing 50,000 bike per year and exporting three-quarters of them to 43 countries, and there’s been a lot of investment to get to that point. But it’s all built around the amazing product.
“We always have new designers come in to work on the bike,” he continues, “and they always say, ‘what about doing this, or that’, and then they end up admitting that, yeah, everything just works on the bike as it is.”
Inventor Ritchie continues: “The path to where we are now was strewn with what seemed like awful setbacks. Yet for each setback there appeared a silver lining, and yes, although a licensee might well have made a good fist of commercialising the bike, I believe that success has arisen in no small measure thanks to my controlling the way the Brompton was made, and presented, to our users.”
One significant change is in the offing with the imminent arrival of an electric Brompton. Sworn to secrecy as we passed through the research and development department, it’s not hard to imagine some of the difficulties involved in adding power to a folding bicycle.
When they’re ready, it’s highly probable that this distinctive little bike will become even more prevalent on city streets as the convenience of getting around on two wheels is opened up to even more potential riders.
And in cities where cyclists still have to fight for their rights on the road, the more of us there are, and the more varied our backgrounds, the better. A suburban commuter eyeing up an electric Brompton as a means to an end might not appear to have much in common with a hardened roadie, but both are helping to tip the balance towards two wheels.
How it all unfolded
Brompton is constantly updating and improving the bike, but these are five key moments from folding history:
1976 — Andrew Ritchie manufactures a prototype Brompton that he uses when pitching the bike to Raleigh.
1982 — Pre-production run of 60 bikes by Ritchie to prove the bike could be manufactured in greater numbers.
1988 — Brompton begins full-time production with two bike options: with a mudguard or with a rack.
2005 — Super-light option introduced with fork and rear triangle made from titanium to shave weight.
2016 — Most recent Brompton bike launched, fitted with new handlebar and gear shifter set-up.