Carbon fiber disc brake rotors are nothing new. Rotors constructed from a combination of carbon and ceramic materials have been used by the automotive and aerospace industries for decades, but the trickle-down to disc-equipped bicycles has been slow and plagued with numerous problems. Two design engineers think they have developed a product that solves these pitfalls while providing substantially better braking performance than anything currently on the market.
Aaron Stephens and Josh Gore are freelance design consultants who have worked on myriad projects ranging from injection molding to packaging solutions to high-pressure regulation. Both are avid cyclists but were outsiders to the cycling industry. The pair tinkered with improving numerous parts on their own bikes—improving dropper seat posts and building better lights for night riding—but it was a serious mountain bike crash three years ago that spurred the creation of Kettle Cycles and lead to the development of their first product: carbon disc rotors.
During a long descent, Stephens’ brakes overheated and failed.
“I was flat out enraged that I spent serious money on these brakes that performed very poorly,” said Stephens. “You’d think that, with the amount of money involved, most of these products would be pretty solid, but they’re not,” he added. “We have the ability to walk into a shop and make something. It’s hard to do that and not turn it into a product.”
Stephens and Gore are far from the first people to attempt to develop carbon rotors for use on bicycles. It has been attempted numerous times since the introduction of the disc brake, yet there are three interconnected problems that have yet to be satisfactorily addressed: rotor thickness, heat dissipation and consistent braking.

Note the absence of holes in the brake track
The thickness, or lack thereof, of disc rotors is a significant hurdle. The materials used have to be quite stiff and, despite the fact the rotors are approximately 2-2.5mm thick, must do an adequate job of dissipating heat.
“If you jumped out to 4mm thick you could successfully use some of the materials that have been attempted, but then you would be creeping up to the weight of aluminum and steel rotors,” noted Stephens.
There’s also the mater of wet weather performance. This has been an issue for those riding road bikes with carbon rims for many years. The same issue has been a stumbling block for the development of carbon rotors. Moisture on the surface and in the carbon itself can significantly degrade braking power. A brief but unnerving “warm up” period is often needed before the pads take hold. Surface treatments are one possible solution, though they have a tendency to wear and degrade over time.
“Our goal from the start was to create a consistent, better-wearing, lighter-weight brake rotor,” said Gore.

With an integrated spider, the SFL (So Freaking Light) rotor weighs a claimed 55g
“Clobbering them with Science”
The answers are as intertwined as the problems. Stephens and Gore claim to have developed a complex blend of materials, manufacturing and chemistry that make their rotors superior to everything else currently on the market.
“We can clobber them with science,” said Stephens.
It’s worth noting that there’s a lot more in Kettle Cycles’ SiCCC rotors than just carbon. The acronym used for the name of the rotors hints in a very general sense at the materials used: silicon carbide, ceramic and carbon. Silicone carbide is used to provide the bite. According to Stephens, this is the ingredient that has been missing from previous attempts. A ceramic compound is used to dissipate heat; the company claims that the SiCCC rotors can tolerate significantly more heat than steel rotors and do a better job of dissipating it, too. Finally, high-grade carbon fiber is used to form the rotor’s structure.
Here’s a video of the rotors in action.
Unable to load Media
Unlike carbon rims, which require specific pad compounds to achieve optimal performance, the SiCCC rotors can be used with standard sintered and organic pads. Stephens says the SiCCC rotors last significantly longer than steel rotors. “We haven’t worn one out yet,” he said.
Kettle Cycles is producing two versions of the SiCCC rotors. The one-piece design, dubbed SFL (short for So Freaking Light), weighs a scant 55 grams for a 160mm rotor, the company claims. The two-piece design uses a carbon spider riveted to the braking track and weighs 60 grams for a 160mm rotor. The 160mm one-piece version is expected to cost $99, while the 160mm two-piece model will retail for $79. The one-piece design is more expensive because it uses more of the costly brake track material. For comparison, a 160mm Shimano XTR rotor weighs 120g and costs $65.
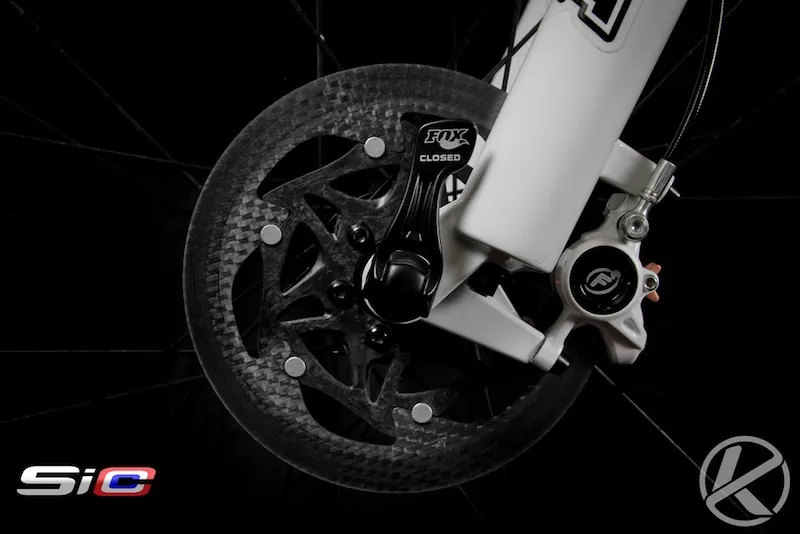
The two-piece rotor weighs 60g with a less-expensive carbon spider riveted to the brake track
Stephens expects the rotors to be available in late winter/early spring, with additional sizes to follow shortly thereafter. BikeRadar has a test pair coming, so check back to read our impressions this spring.
Kettle Cycles is not keen to stop at brake rotors; carbon cranks, dropper seatposts and carbon frames could all be future projects.
What do you think? Would you choose carbon rotors over steel?