It is a poorly kept secret among craftsmen frame builders — the less riding you do, the more bikes get built.
"There’s an inverse relationship between our fitness and how much we're getting done in the shop," said Aaron Barcheck, who founded Mosaic Hand Crafted Performance Bicycles in 2009. And much to the satisfaction of a few hundred riders who have purchased custom titanium or steel frames from Mosaic, Barcheck hasn't had high-level fitness for a while.

Barcheck's years of experience pay off in the careful details
But for Barcheck, who spent seven years as a builder for Dean Titanium Bicycles, the process of working with riders to create their dream machine is completely worth the effort. Here, Barcheck walks us through the process of creating a frame inside his workshop in Boulder, Colorado.
Mosaic makes steel and titanium frames for road, mountain, cyclocross and track.

After a lengthy interview, a drawing is creating
While the end product is obviously a bicycle, a big part of what Mosaic sells is the process of a a rider working with an experienced builder — and often with an experienced fitter at a bike shop — to refine what a perfect bike would be for that individual.
"The conversation starts on what they want out of their bike," Barcheck said. "The interview process is a big part of what we do."
Kevin Batchelor works alongside Barcheck at Mosaic. Often the interview process is done through an expert fitter at a shop. "And everything is made specifically for that rider: geometry, tube thicknesses and diameter, ride quality and aesthetics."
Sometimes Barcheck will heavily steer the discussions on geometry.
"Some riders have a really good idea about what they want... and they’re right. And some have a really good idea, but they could use some direction," he said. For example, some riders insist that they want a really fast-handling bike, "but if they are asking for 56mm of trail, we'll talk them into 58." (For reference, 60-62mm of trail is the sweet spot for road bikes, Barcheck says.)
Once the shop or Mosaic has a rider's fit data and other information, the company will create detailed frame drawings with every angle and every tube measurement detailed. Once the bike shop signs off on the drawings, it goes into the build cue. Turnover is about six weeks.

Mosaic machines metal on a lathe to transform a piece of pipe into a sculpted head tube
First, Barcheck pulls all the tubing and parts needed for a frame. The tubing is cut on various machines, with every angle and diameter specified from his drawings. After cutting, each piece is touched up with careful grinding to ensure a precision fit. "That's where the experience hand really makes a difference," Batchelor said. "Tight miters make strong bikes."

Mitered joints are carefully cut at the angles and lengths prescribed from the frame drawing
After this, each frame piece is washed with acetone, then mitered together in the fixture below. "We do a single pass of a fuse weld while the frame is in the fixture," Barcheck said.
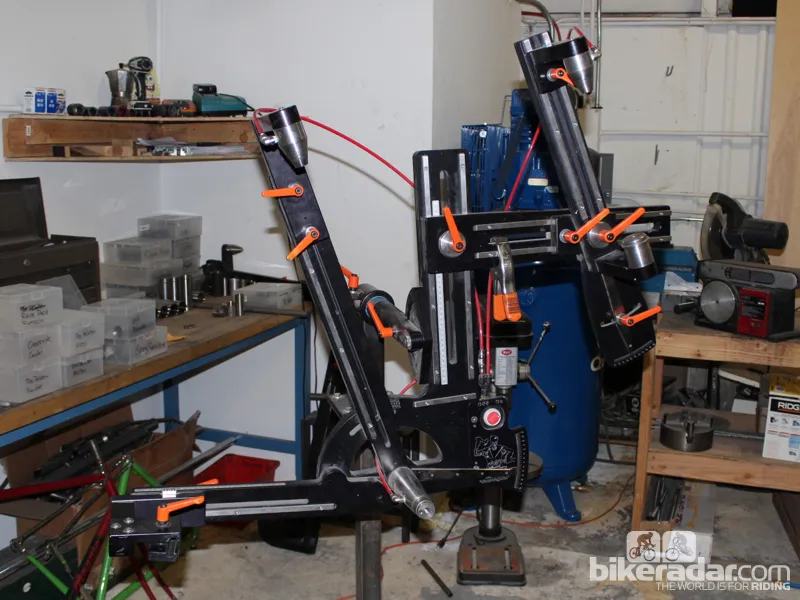
This Anvil Journeyman fixture holds each piece of the frame in place
Next, bridges, bosses and stops are welded on and each joint is carefully secured during the finish-pass welding, which takes about two and a half hours. For titanium frames, Mosaic welds with a steady flow of argon, an inert gas that keeps oxygen away from the hot metal.
"Oxidation is the enemy," Barcheck said. "And titanium is particularly sensitive."

Head tube angle (shown here) and bottom bracket drop are accounted for in the easily adjustable jig
"Frame alignment for ti is all about the building process," he said. "If all the miters are tight, you can weld at a really low heat."
After the frame is fully welded, Mosaic runs it through a quality control process, and machines everything out to spec, facing, chasing and reaming the head tube and bottom bracket.

A finished weld
Once the frame has been QC approved and prepped, Mosaic then completes the finish. Frames that require paint are shipped to Spectrum Powderworks in Colorado Springs. Nude frames are finished with bead blasting, where Mosaic sprays the metal with sand for an even finish.

Each frame is bead blasted for a uniform finish
One treatment Mosaic does is a polished logo on a matte frame, show below. For this, a polished section of the tube is masked in the shape of the logo. Then the frame is bead blasted, and afterward the masking is removed, leaving the logo behind in polished detail.

This striking logo is created by masking the logo outline over a polished tube, then bead blasting the unmasked sections
After a few years in business, Barcheck estimates that Mosaic will make 100 frames this year. "If I work my butt off for the next few weeks," he said.

Batchelor's personal bike features an integrated seatmast, Campagnolo EPS and Enve wheels
"Our goal is to be a big, small company," Batchelor said. Mosaic currently works with six shops, for of which are outside Colorado. And riders can buy directly through Mosaic, too.
Custom titanium frames start at $3,000, and steel frames start at $1,900.
For more information, check out MosaicCycles.com.

Team Small Batch is a cyclocross team with handbuilt bikes. But really, every Mosaic bike is made in a very small batch... one at a time