To mark the relaunch of Univega in the UK we were invited to the huge Derby Cycle factory in Germany where the bikes are built, along with models for Focus, Kahlkoff and domestic brand Rixe.
Based on the outskirts of Cloppenburg, an hour or so's drive from Bremen, the first thing we noticed at the factory was the huge employees' bikeshed and enormous adjacent car park – as one of the top three bike producers in Europe and Germany's market leader, these guys mean business.

Our visit coincided with Derby's annual dealer launch and they were expecting representatives from over 1,000 German shops to turn up the next day to check out the 2010 bikes and tuck into an ox- and hog-roast. As a result the plant was a hive of activity and hundreds of new bikes were lined up in the main hall, along with a couple of curiosities.
On the way in our attention was caught by this little beauty, complete with beer bottle holder above the bottom bracket.

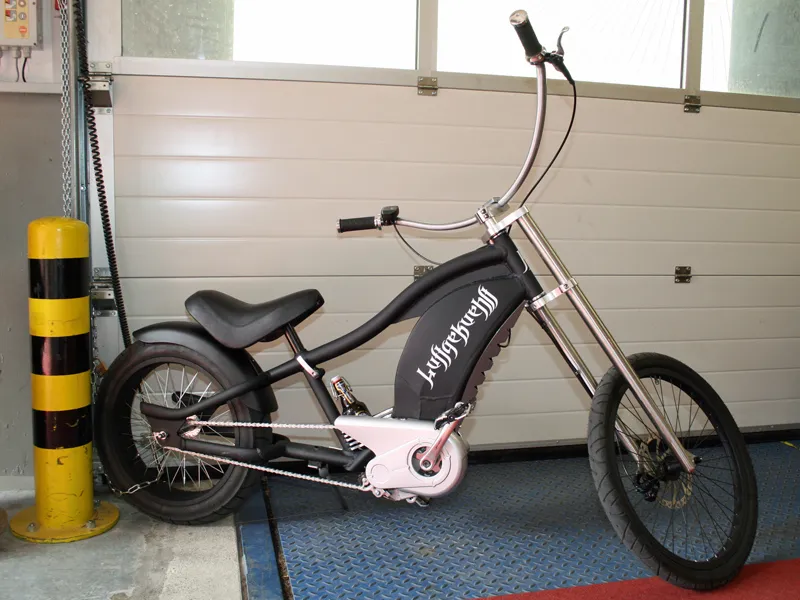
This tandem complete with internal cable routing and adjustable dropouts was also drawing lots of admiring glances. It weighs in at 19.5kg (43lb). Bet the ride's a little wooden though...

Terrible puns aside, it was made by Zeidler Holzkunst GmbH and Jens Eichler from beech, it's called 'Renovatia' and the finish really had to be seen to be believed.

To give you some idea of the size of the Derby Cycle complex, we were led along a corridor housing the engineers and accountants' offices that's 200 metres long.
Testing, testing...
The guys from Univega were keen to impress on us that although their bikes are priced competitively they don't cut any corners when it comes to testing and manufacturing, and this was evident as soon as we entered the lab.
It's full of an array of machines designed to test every single part of a bike – right down to kick-stands and pannier racks – to the limit.
Derby's head of marketing, Herwig Reus, told us: "I don't believe anyone else in the world has anything comparable to this."

Random samples of every component used on every bike are put through tests designed to simulate 10 years of normal wear – twice the EU standard. Then the finished bikes are tested too.
Unable to load media
One of the most impressive devices was the drum test machine for high-end mountain bikes. The sample bike is weighted down (52kg on the saddle, 36kg on the pedals, etc, up to a total of 102kg) and held in position over two metal drums. These revolve at 15-16km/h under the wheels to simulate movement.
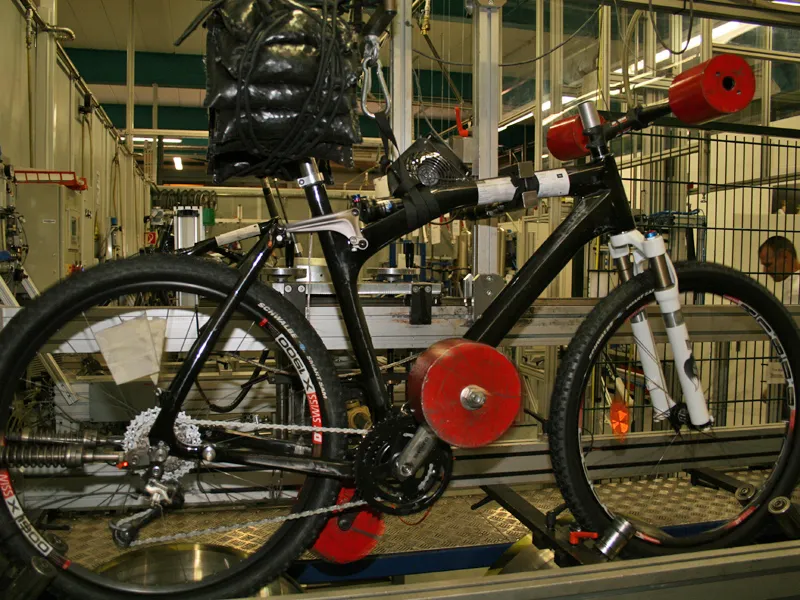
To test the durability of the bike's frame and suspension, retractable bars on the drums can be raised to simulate obstacles. A full-suspension bike has to withstand 90 hours with the bars alternated between 36mm (1.4in) and 12mm (0.5in) high. A fan is used to prevent the rear shock from overheating.
Handlebars are tested using a machine rigged up to a computer which pushes both ends of the bar down with 1,700N (approx 170kg) of force. Even the beefiest downhill mountain bike bars flex by up to 30mm (1.2in). Bars are tilted forwards and backwards to simulate climbing and descending.

Headsets are put through one million turns and must not suffer any fractures or damage to the race, while fork legs are bent backwards using up to 1,000N of force. Parts are also put through salt water and sunlight tests to check their durability. Check out the thumbnail gallery at the top of this story for more images from the testing lab.
Assembly
Univega's frames are made in the Far East, but everything else is done in-house in Cloppenburg. Right behind the test lab is a warehouse full of frames and bike parts.
Most bike companies respond to customer demand, so they produce a certain number of models at the start of the year and if one proves particularly popular it sells out and customers have to weight months for more parts to be ordered and more bikes to come into stock.
At Derby, they do things differently. They do a precise forecast for the whole season and start buying well in advance. As a result, there is around €16 million worth of components in the warehouse at any time, and they get through 1.1 million wheels a year.

Derby also practise what they call 'nest' production, whereby as many parts as possible are put together before they reach the bike assembly line. For example, cables and chains are cut to the right length, and shifters, brake levers and grips are slid onto handlebars.
Every frame is checked by hand to make sure it is properly aligned. Any imperfections are sorted out the hard way before it is cleaned and then goes on to the next stage of the assembly process – painting.

All bikes are powder coated, with critical parts done by hand. They are then painted with a water-based colour before being powder coated for a second time. This means the bikes have a car industry level of finish.
If the frame has more than one colour, the additional hues are applied by hand. Bikes are carried around the factory on a 1.6km-long chain.

Spokes are one area where many companies cut corners, but not here: they're all from either DT Swiss, Sapim or Alpina.
Hubs are put into a machine which automatically inserts spokes into all of the flanges. Wheels are then laced by hand before going into another machine to be trued. Each wheelset takes 12 minutes to build.
Unable to load media
Finally, bikes are assembled. German customers are among the most demanding in the world, with a meticulous eye for detail, and all bikes are shipped fully built.

Aladdin's den
At the end of the tour we were led outside to an area where last year's leftover parts were being sold off cheap to German shops. With rear shocks from €2 and carbon forks from €20, there were some amazing bargains to be had.
